Your cart is currently empty!
Relishing the Accelerated Completion: Harnessing Six Sigma for Rapid Goal Accomplishment
Leveraging Six Sigma’s streamlined routes to achieve objectives quicker.
Six Sigma’s DMAIC (define, measure, analyze, improve, and control) framework is utilized to steer process enhancement endeavors. However, these steps may not always follow this simplistic order. Occasionally, it’s feasible to take an expedited route to the control stage. The objective is to attain the project’s target, consuming the least possible resources, assuming the project’s goal aligns with the overarching goals and objectives of the organization.
At times, a team might realize that the process works optimally once the metrics are outlined and a measurement system is instituted. I’ve come across numerous processes where all the measured variance resulted from measurement errors. When this happens, process variance becomes inflated as individuals alter the process based on these inaccurate measurements. Remove the measurement system error, and voila! The process meets customer requirements without further action.
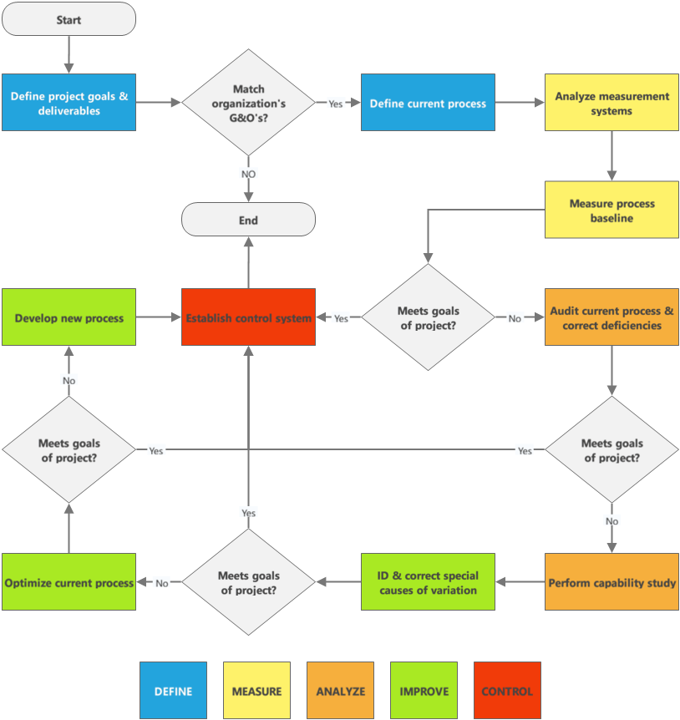
It’s vital to remember whose requirements you’re fulfilling. Internal requirements should invariably be extracted from customer preferences and necessities. Nevertheless, Six Sigma teams often uncover that several product requirements bear no relation to what customers genuinely value. Here’s an illustration:
A solar panel manufacturer, specific to a particular application, load-tested the panels to 950 pounds, where 10 percent of the panels failed. Extensive field data gathered by a Black Belt showed that in service, the panels were never subjected to loads beyond 750 pounds. The load-test specification was modified to 825 pounds, ensuring a 10 percent safety margin. The result was a disappearance of test failures and no observed field failures.
The race for swift gains can sometimes result in implementing processes that are not yet ready. Process designers are often engrossed in various tasks and may move forward once the process is running “adequately.” But this doesn’t imply it can’t improve further.
I mentor Black Belts to lead their Six Sigma teams to develop an additional process map, known as the “should be” map. This map delineates how the team believes the process should operate. Utilizing the should-be map, the team constructs a set of criteria on one or more check sheets. With these check sheets, the team performs an observational study. They actively venture into the workspace to observe the actual conditions. Often, the reality is not as satisfactory. The noted deficiencies are then integrated into a corrective action plan. Here’s an instance:
A team investigating shipping damages found issues occurring even before packages were loaded onto trucks. Packages were stacked chaotically, leading to stacks toppling over and boxes at the bottom of heavy stacks getting crushed. The root of the issue was the incomplete staging area, deviating from the original design that included shelves, racks, and conveyors. Upon finally installing these, almost all damage was eliminated.
Another route to the goal utilizes statistical process control to identify and eliminate specific causes of process variation. This can best be achieved through a process capability analysis (PCA). The PCA will supply a set of statistical guidelines indicating when the process is influenced by an abnormal operation. Responding to these signals enables the process operator to pinpoint the problem’s source and either address it or seek assistance. Eradicating these problems’ root causes often suffices to meet project goals.
My final shortcut involves using design of experiments (DOE) to scrutinize the current process by pushing diverse factors to their boundaries and monitoring the effect on the process output. The DOE is a sequential procedure that systematically guides the process to its peak performance. Upon reaching this point, compare the outcome to the requirements to ascertain if the goal has been achieved.