Your cart is currently empty!
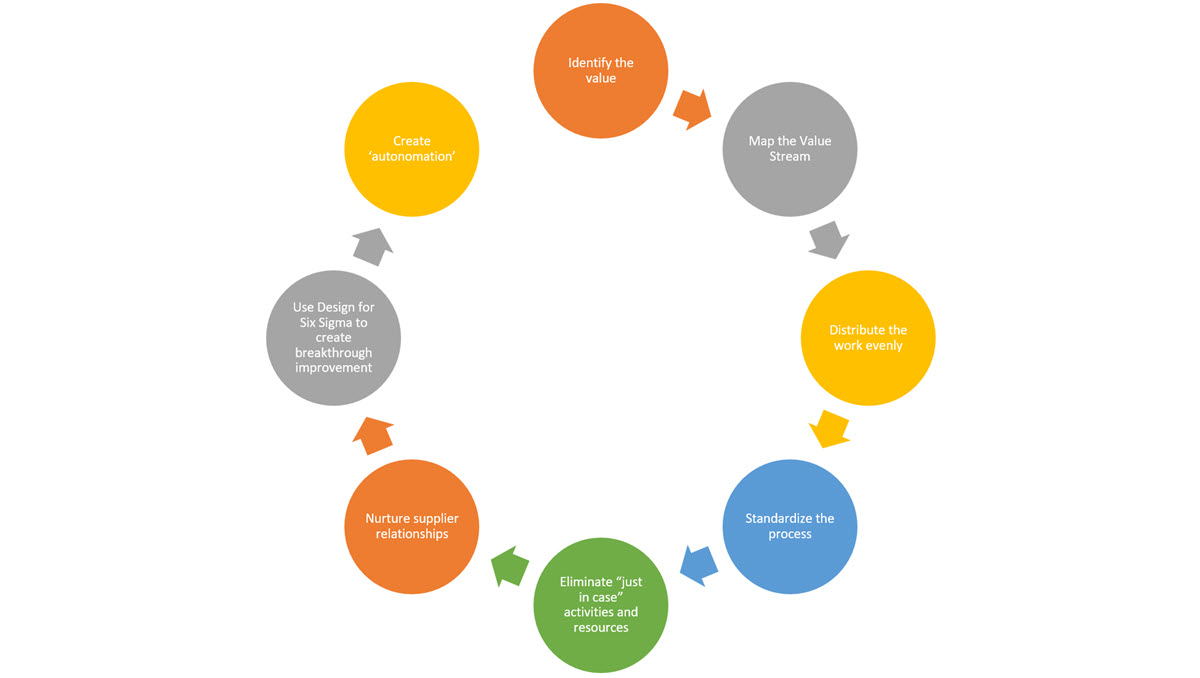
Becoming a Lean Organization in Eight Steps
Becoming Lean: A Tactical Perspective
At the strategic level, becoming Lean involves a culture change. An organization ready for Six Sigma is also ready for Lean. However, there are some differences in the deployment of the Lean model. Becoming Lean requires an organization where continuously improving is part of the culture. Here are some guidelines for deploying Lean at the process level.
- First, identify the value. Use all known means to determine what existing and potential customers really want.
- Next, map the value stream. Identify how work flows to create the value. Determine how information flows to support this process. Identify non-value-added activities and set goals for reducing muda.
- Distribute the work evenly. Balance the process.
- Standardize the process. Identify the core process and eliminate steps needed because of unpredictability by minimizing variation, errors, and defects.
- Eliminate โjust in caseโ activities and resources. Schedule Just-in-Time deliveries. Stop ordering extra items to deal with uncertainty. Stop hiring temps or per diem workers to deal with unexpected problems.
- Nurture supplier relationships. Bring the supply chain into the design of work processes. Integrate their delivery and information systems with yours.
- Use Design for Six Sigma to create breakthrough improvement. Remember, you donโt create products or services, you create customers. Disregard your investment in existing assets and systems and develop entirely new ways to serve your existing customers better, and to create new customers.
- Create โautonomation.โ Autonomation is a word invented by Toyota executive Taiichi Ohno to describe a production system that mimics the human autonomic nervous system. It automatically adjusts to external and internal conditions. For example, when we get too hot, our body automatically reacts to cool us down; we donโt have to think about it. Similarly, production and service systems should react to customer demands, increasing production when demand goes up or decreasing production when demand goes down. They should automatically react to Work-in-Process inventory buildup by producing less or producing on a different schedule. Lean mechanisms to accomplish this include Takt time, visual controls, pull systems, exploiting constraints, etc.
3 responses to “Becoming a Lean Organization in Eight Steps”
On the subject of Taiichi Ohno, I’d point out a lost opportunity made by Lean organizations.
When standing in the Ohno Circle (a superb exercise for nearly any process), don’t look just for process waste, look for sources of process variation. Two for the price of one!
I’d further add that a “Lean Mindset” is a pre-requisite to the 8-step process.
If the corporate mindset is “push it out the door as fast as possible”, then Leadership will have to re-calibrate the corporate mindset first before embarking on the 8-steps.
I love to read the 8-step process and step 7 may be one of the best steps in my opinion.
There is no question about having “Lean Mindset” as a must for the 8-step process.
Leave a Reply