Your cart is currently empty!
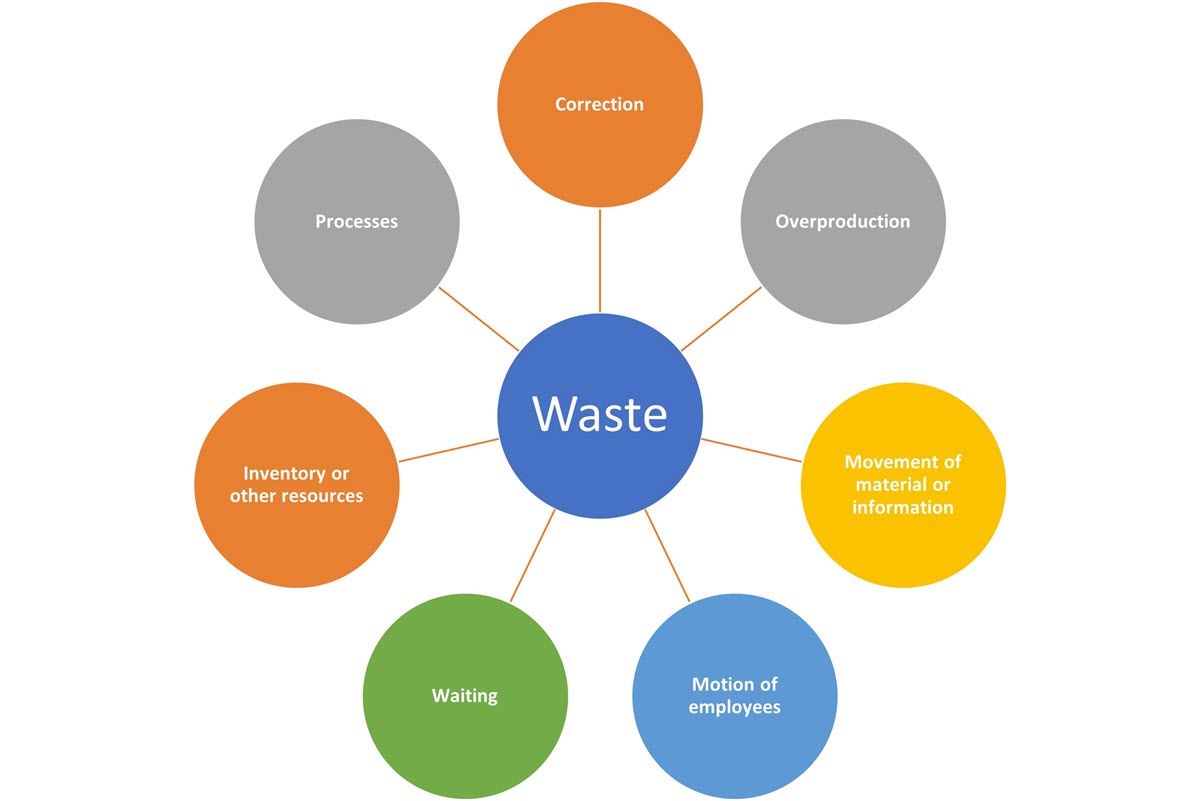
The Seven Types of Waste in Lean
I have written several articles about the seven types of waste in Lean. Here’s a comprehensive list of these wastes, along with brief descriptions.
The Seven Types of Waste
- Correction: Corrections entail redoing, rewriting, reworking, repairing, or scrapping anything. A simple example could be rewriting a grocery list in the order of the items in the store. Though it may make shopping quicker, rewriting the list is a non-value adding activity. It could have been avoided by correctly organizing the list the first time.
- Overproduction: Overproduction occurs when you create excess products or perform more of a service than required. An example is making extra copies for a meeting that eventually get discarded. Overproduction can also happen when a salesperson provides more information than necessary in response to a customer’s simple question.
- Movement of Material or Information: This waste involves moving any material or information from one place to another. Whether you ship it or carry it yourself, this movement does not create any value for the customer. In fact, it can delay your product or service from reaching your customer.
- Motion of Employees: This waste occurs when an operator has to walk or travel to get something to perform their job. Like the movement of materials and information, an operator’s motion does not create value.
- Waiting: This waste occurs when you, other employees, customers, material, or equipment sit idle waiting. Think about all the waiting rooms out there. As a customer, nobody wants to wait, but sometimes we’ve come to expect it.
- Inventory or Other Resources: This waste isn’t just about supplies and materials on shelves. It also refers to any resource in your company not being utilized, such as idle equipment or underused employee skills.
- Processes: This waste occurs when you’re doing more than what the customer requires. It’s important to understand what is of value and what isn’t. At times, we might do something extra for the customer that they do not appreciate. That’s when it becomes a waste.
Leave a Reply