Your cart is currently empty!
Lean Six Sigma Improvement and Work Design
This article is an excerpt from a lesson in Pyzdek Institute Lean Six Sigma Black Belt training. Future posts will continue the topic.
In previous lessons you learned how to change a traditional batch-and-queue value stream into a lean value stream. Now we will discuss the design of the actual work that will take place within the processes of the value stream. By going a level deeper we will be able to improve the flow of work within the different processes in the value stream. Specifically, you will learn how to design continuous flow work cells. While the discussion here focuses mainly on manufacturing work cells, the lean principles described apply to any work, including that done in administrative, transaction, or services such as healthcare, retail, and so on.
Selecting Subprojects
The first step is to identify subprojects within the value stream. Subprojects, sometimes called project โloops,โ are determined by looking at the future state value stream map and choosing groups of related processes in the value stream for improvement analysis. Each subproject will require a different team with its own set of knowledge, skills, and abilities. However, it is desirable to have at least one member of the Lean Six Sigma team who participates on all of the subproject teams. Figure 1 shows a future state value stream maps with subprojects identified.
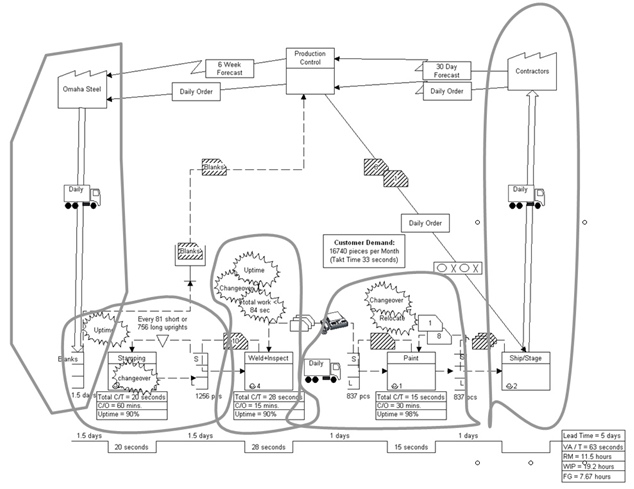
Once subprojects are identified, the Lean Six Sigma team must decide which to pursue first, second, and so on. As a general rule it is a good idea to begin at the customer end of the value stream and work backwards. This provides the customer with improved service that they can see and feel quickly. Another criterion is that the pacemaker process should be improved early, since it sets the pace for the rest of the value stream. The โInside-Out Ruleโ should be observed: get your own house in order before extending your improvement efforts to include the value streams of outside customers and suppliers. Of course, your decision regarding the starting point should also take into account the likelihood that the subproject will have a big impact on the business and its customers.
Donโt think of the future state value stream map as untouchable. If, as you go through the exercise of selecting and prioritizing subprojects, you see an obvious improvement thatโs not on the map, revise the map. Remember, the goal is to improve as much and as quickly as possible.
Once the subprojects have been identified and prioritized, treat each of them as you would any project. You may want to review the modules covering project management in the Define phase at this time. For each project find a sponsor (the value stream owner is a good candidate,) write a charter, select a team, develop a schedule, identify stakeholders, etc.. By now these things will be second nature to you.
Elements of Work
Figure 2 shows the relationship between value streams, processes, operations, workplaces and procedures in the creation of value. The relationship is hierarchical. To implement Lean all levels of the hierarchy are considered. In previous lessons we discussed ways to change value streams by replacing batch-and-queue push scheduling systems with lean value streams where work is scheduled to maximize flow. Several other lessons focus on ways to improve processes, the next level of the hierarchy. For example, by using process maps to see how work flows through processes or by identifying non-value-added work. In designing work cells we will go deeper than the process level and look at the design of operations, including the layout of workplaces and the standard procedures followed to perform the work in each operation. Such operations are known as standard operations, because the way work is performed follows strict standard procedures.
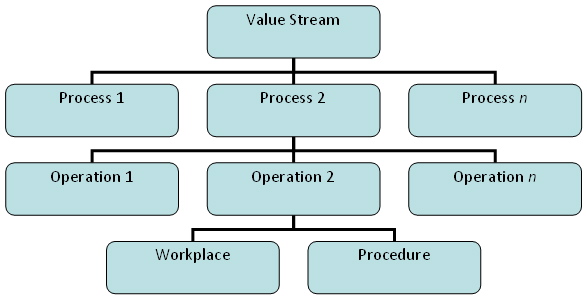
Processes are distinct sets of operations nested within a value stream. Process improvement has been the topic of numerous lessons in this course and it requires knowledge of the root causes creating process problems. In the context of designing continuous flow work cells in Lean Six Sigma, we focus primarily on the things in a process that inhibit flow, such as
- Non-value added process steps on the opportunity map
- The distance people, materials, or WIP travel between process steps (from the spaghetti chart)
- Changeover, setup and adjustment time (discussed below)
- Identify the root causes that are creating quality issues that are responsible for scrap, rework, or problems downstream (discussed in later modules)
In Lean Six Sigma we design work cells that improve the process as well as the specific operations within a cell. We get into โnitty-grittyโ details of the work itself, considering how materials are handled and moved, fixtures, workplace layout, movement of various workers, etc. The transfer of work elements (small units of work) between workers is carefully considered. โWorkโ is the sum of all of the work elements required to create one complete unit through the entire value stream.
If you are interested in Six Sigma Certification and Training, contact Pyzdek Institute today!
Leave a Reply