Your cart is currently empty!
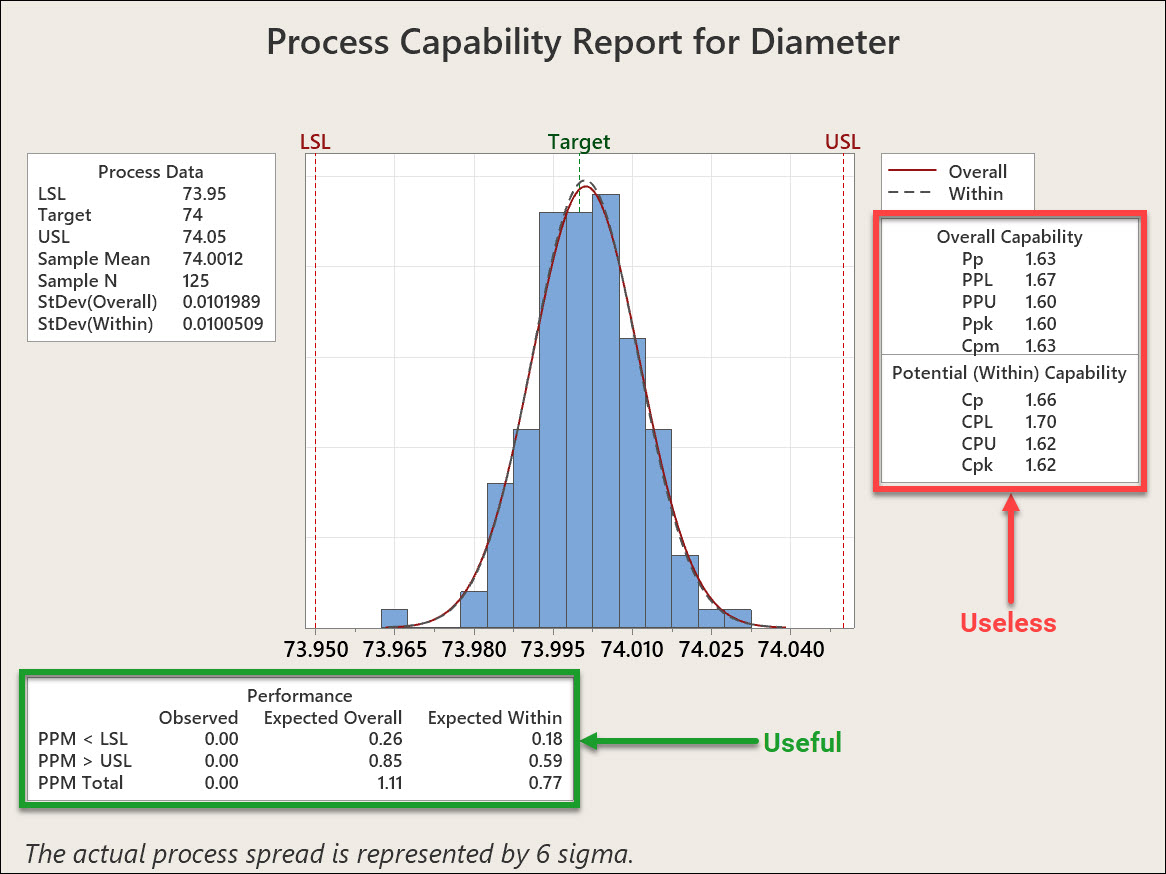
It’s Time to Ditch Process Capability Indices
Process capability indices (PCI) have long been popular with many quality professionals. But they’ve also been controversial and a number of reputable experts have advocated that they be abandoned.[1] I tend to agree. Maybe it’s time to ditch process capability indices. Here’s the good, the bad, and the ugly of PCIs.
The Ugly of PCIs
- Often misused. The number of ways to misuse a capability index are legion. For example, calculating the index for a process that is not in statistical control or for a process that isn’t even approximately normally distributed. These indices are useless at best, misleading at worst.
- Often misunderstood. Cp, Cpk, Cpm are hard enough for a quality engineer to understand. Lay people often have no clue as to what they mean in the real world. Nor should they need to know.
- Gamed. Process capability indices can be deliberately manipulated to make a result appear the way an unscrupulous supplier or manager wants. For example, conducting a capability study over a time interval that is too short to show the impact of multiple potential special causes. Or assuming normality when the metric is not normally distributed.
- They are only useful for a single metric. Capability indices apply to a single process metric. But products and services are complex and involve dozens of performance metrics.
The Bad of PCIs
- They don’t work for unstable processes. In all fairness, you really can’t make any predictions if a process isn’t in statistical control. Nevertheless, PCIs are often reported for unstable processes. In fact, it can be said that Ppk, which is calculated using “long term sigma,” are pseudo-estimates of Cpk for possibly unstable processes. Short- and long-term sigma will be approximately the same for stable processes.
- Complicated and confusing. PCIs combine customer requirements, process mean and process spread into a single number. It’s made-to-order for confusion.
- Provides no direction about how best to improve. OK, your PCI isn’t acceptable, how best to improve? Reduce variation? Recenter the process? Reconsider the engineering specifications? You can’t find the answer in the PCI.
- Not a good replacement for process yield metric. Process yields and rolled-throughput yields are the metric we often really need. PCIs are no help in estimating these.
- Confidence limit calculations complicated but needed to grasp the significance. Many academic papers have been written describing and discussing confidence intervals for PCIs. PCIs are a veritable full employment plan for professors and academics. As for the engineer and business user, not so useful. But without knowing the distribution of the PCI we can’t know the uncertainty associated with it. Catch-22.
The Good of PCIs
- Work okay for stable, normally or approximately normally distributed processes. If you have this situation, good for you. But wouldn’t an estimated yield give you the same information in an easier to understand metric?
- Distills several metrics into one. This is both good (fewer is better, right?) and bad (it provides no guidance if it’s bad).
- Some PCIs are better than “goal posts”. Some PCIs are use process targets and show the value of continuous improvement. A PCI based on goal-post specs provide no incentive to improve if nearly everything is between the goal-posts.
- Free of measurement units. PCIs for different metrics based on different units of measure can be compared.
The Baby in the Bathwater
Process capability studies are extremely useful. An absolute requirement for estimating process capability, whether you plan to use PCIs or not, is a stable process. Determining that your process is stable involves performing a process capability study. If your process is stable and its output meets or exceeds the customer’s requirements, maybe calculating and reporting the PCI is an unnecessary complication.
[1] Pignatiello, J.J., Ramberg, J.S. Process capability indices: Just say no! in: Proceedings of. the 47th ASQC Annual Quality Congress, Boston.
2 responses to “It’s Time to Ditch Process Capability Indices”
-
This is a great summary of the limited usefulness and common pitfalls of process capability indices.
I agree, making business decisions with a Cpk index without a confidence interval is fraught with danger. For what it’s worth, I’ve seen the following Cpk confidence interval approximation used for normally distributed data:
Cpk /- t*sqrt(1/9N (Cpk^2/2N-2))
This approximation clearly indicates we need a lot of representative data for a meaningful index.
-
I agree that if a process is unstable, then any PCI has little value. But if the process is unstable then does a process yield, the suggested alternative to PCI’s, have any value either? If the process is not stable, nor appx normal then that needs to be addressed, where possible, or an alternative PCI should be used. This assumes that the metric under consideration is of value. Thanks to all the automated data collection processes, we now have reams of data, but no information.
If a QE cannot explain the meaning of the various PCI’s so that a lay person can understand, s/he needs to get training or find another job.
As for what to improve, process yield does not answer that either, letting mgmt revert back to their old exhortations “Just do better”. If QE’s would like some help, I suggest they read the first article in the newsletter regarding the Benefit Effort Matrix.
The best argument that I have for a PCI is that under proper conditions, it, as noted, drives the process to produce similar product at nominal. And continuous improvement needs to be the mindset. The downside of a process yield metric considers all product between the goalposts to be of equal value (football mindset). The fallacy of that thinking is apparent when you take two parts, one a smidge inside the goalposts and one a smidge outside the goalpost, assuming MSE=0. (I recall a manager telling the tech, “Go measure/test it again. If it is in spec then it is good.”) From the goalpost thinking one part has complete value, while the other one has no value. In reality the performance of the two in whatever operation it goes into, will essentially be the same.
For a real life example that contrasted these two approaches, I recommend going back to the Ford Batavia transmission plant analysis from the late 70’s or early 80’s.
Bringing it closer to home, if you needed brain surgery, with all other factors being equal, would you rather have the surgeon who aced his brain surgery exam and practical–at nominal–or the one who squeaked through with the lowest possible grade–inside the goalpost. (School exams DO presume MSE=0, when we know that is not the case.)
Leave a Reply