Your cart is currently empty!
The Truth About Inventory Waste
This is Part 2 of the Pyzdek Institute Lean Concepts Study.
To recap from Part 1: We are all fortunate to have the accumulated knowledge of manufacturing industry titans to help us improve processes and reduce costs. In the Lean context, Taiichi Ohno and Shigeo Shingo stand out. They taught us much about the process improvement mindset, visual control systems and the like. Both indicated the need to relentlessly identify process waste and do something about it. We started with the list of 7 Deadly Wastes and eventually added safety and wasted talent as Deadly Wastes #8 and #9.
In the spirit of continuous improvement, The Pyzdek Institute proposes taking that list even further.
The Original List
1) Transport | 6) Over-production |
2) Inventory | 7) Defects |
3) Motion | 8) Safety |
4) Waiting | 9) Under-utilized talent |
5) Over-processing |
Improving the List
We propose adding other forms of waste to this list and we’ll cover the particulars of the list expansion in future blogs. One example is the waste of bad data.
Meanwhile, to benefit Lean Thinkers everywhere, The Pyzdek Institute has accumulated real-world examples of The Nine Deadly Wastes to make available to Lean Thinkers everywhere. To that end, please post in the comments section below any examples that you’ve encountered. We’ll add them and in the future, we’ll post downloadable documents to the Pyzdek Institute website. Additionally, please highlight examples where one form of waste causes another (see last bullet point below).
A Brief Overview of Inventory Waste
While some stock of material may make business sense, excess stock of finished product, in-process product and raw material are considered Inventory Waste. An example is excess raw material inventory in place to get “volume discounts”. This approach to inventory management might make the purchasing budget look good, but there are significant financial consequences. These consequences almost always outweigh the benefits:
- ties up capital
- vulnerable to degradation
- vulnerable to obsolescence
- usurps valuable floor space from value-added processes
- consumes energy
- consumes labor
- more theft
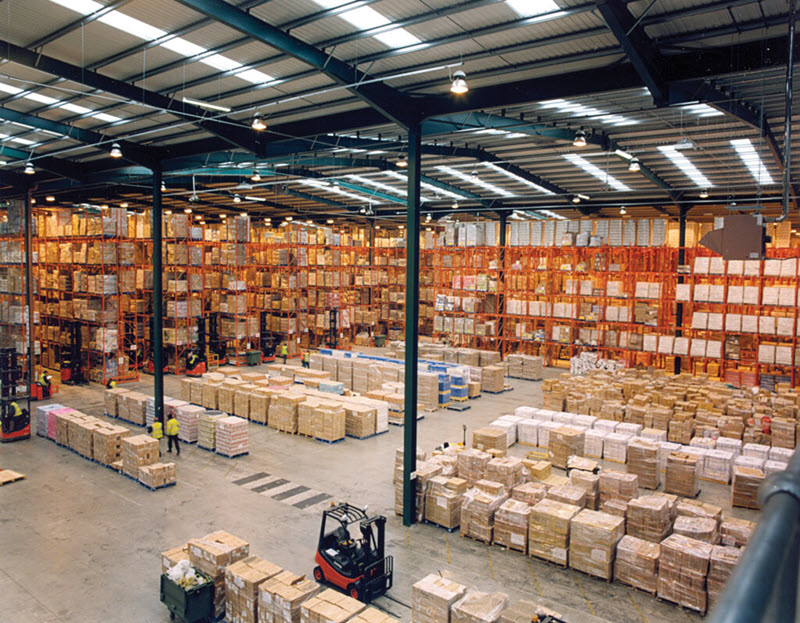
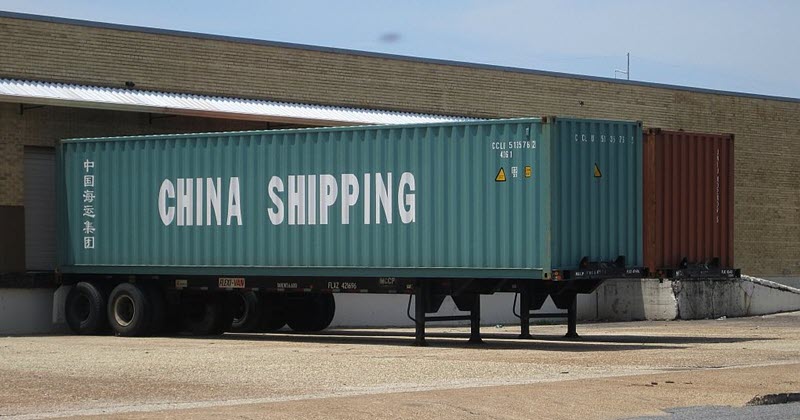
The root causes of Inventory waste include a poor understanding of demand, unstable processes and a poor understanding of the cost of capital. Inventory waste is easy to identify, it’s all the material that doesn’t move. Inventory waste can have a devastating effect on safety. Examples include pallets that are stacked in an unsafe manner and leakage of liquid raw material due to container degradation. Inventory waste can have a devastating impact on profits. Examples include the high cost of buildings and other physical plant and the high cost of labor to manage excess inventory.
In addition, inventory waste hides other forms of waste. Examples include the use of inventory to account for a problem with defects and the use of finished goods inventory as an expensive countermeasure for raw material lead times.
Inventory Waste Examples
- Warehouses full of excess raw material
- Forty foot rented shipping containers full of excess raw material
- Warehouses full of excess finished goods (Sales said we’ll sell it before the end of the quarter “for sure”)
- Rental of additional warehouse space to store excess finished goods
- Excess office supplies
Inventory Waste that Creates Safety Hazards & Defect Waste
- Line-side raw material creates tripping hazard
- Line-side raw material chaos results in wrong material selection (I don’t have time to get that material!)
- Overloaded shelves (but where else can we put it?)
- Additional fork truck and pallet jack traffic
- Toxic byproducts from material degradation (anti-microbial additives no longer effective…)
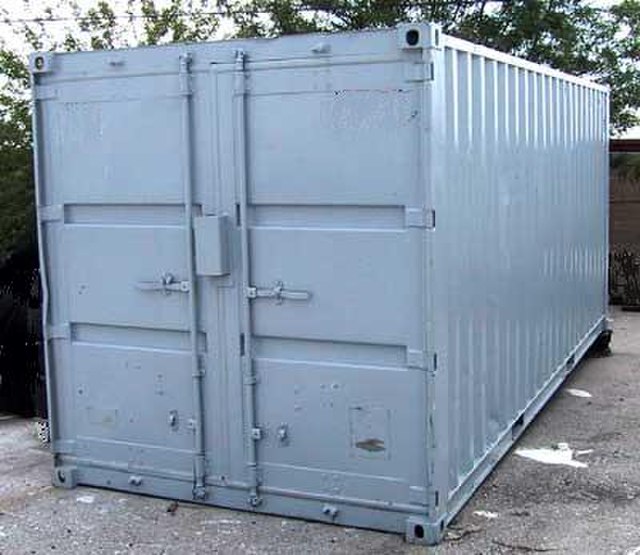
Meanwhile, we have effective countermeasures readily at hand. First, abandon the batch & queue mentality in favor of pull-based production. Second, improve work cells using 5S and cellular layout. And, consider staffing and other variables that provide steady product flow.
The #1 Countermeasure to Inventory Waste
Finally, experience shows that the best countermeasure to inventory waste is rarely taught in Lean Training classes. As it turns out, Statistical Process Control plays a vital part in the reduction of inventory, over-production and other forms of waste. Without control charts, we don’t hear the Voice of the Process. Without hearing the Voice of the Process, complex production processes remain vulnerable to the influences of outside forces. The consequences often appear only after the customer has the product in hand. But with the persistent use of control charts, we can act immediately when a change occurs. With a stable process, manufacturers can reduce all forms of inventory waste.
As a friendly reminder, please add your examples of Inventory Waste in the comments section below.
Next time: Motion waste
3 responses to “The Truth About Inventory Waste”
-
Here’s an example of Inventory Waste.
In the Medical profession, it is common for staff to horde things because sometimes inventory runs completely out and it takes weeks before supplies arrive. The delay is often due to the laborious purchasing process and a poor understanding of usage rates. In one maddening case, a Purchase Order for a critical item was delayed because one of the (many) approvers was out on medical leave and a backup hadn’t been appointed. In this case the waste is because of a lack of product instead of too much product.
The solution, of course, is to study consumption patterns, simplify the purchasing process and to get the materials needed without tying up capital (all those instruments hidden away tie up a lot of cash!).
Why does a Purchase Order for an item that is used all the time have to be approved by multiple people.
-
Steve covered a very good review of inventory waste and showed us how to countermeasure to the waste with just the short article. Thanks Steve.
Agreed that “Under-utilized talent” is one type of waste as I have witnessed in my working experiences.
For example, there are good ideas or thoughts of how to improve processes contributed by employees who are experts of what they are doing. These good ideas normally are put in the queue (inventory) and unfortunately there are no review of management to make them into action. It turned out that these good thoughts get lost and companies miss the opportunity to improve their processes and save cost. -
Thank you to everyone that commented. If you have any other example, please post them.
Steve
Leave a Reply