Your cart is currently empty!
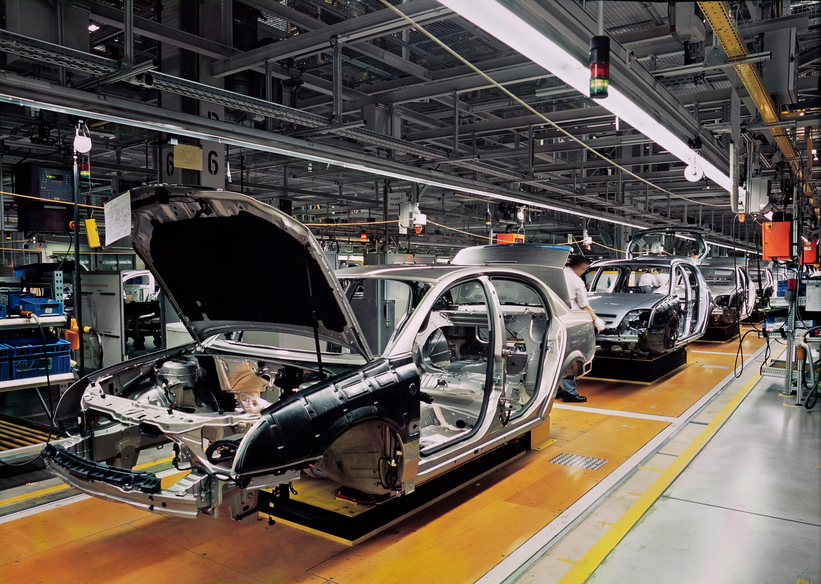
A Flashback to the Early Days of Lean
Lean operations or lean manufacturing (often referred to simply as lean) has become a buzzword in the last 15-20 years to describe the goal of continuously improving operations, primarily by minimizing waste. But how did the movement start? Let’s delve a bit deeper into this area and take a look back at the early days of lean.
Dr. W. EDWARDS DEMING
W. Edwards Deming was an American business and manufacturing consultant who helped revolutionize the manufacturing process. His”14 Points of Management” played a huge role in changing the way companies looked at operations in general; the irony was that although Dr. Deming was an American, his ideas were adopted much more readily and earlier in Japan than in the United States. His ideas helped form the basis of many basic tenets of lean operations, and of his myriad quotes lends some insight into his theories: โWhat state of a company is in the best position to improve quality? A healthy company is in an excellent position to improve and has the greatest obligation to improve. A company on the rocks can only think of survival.โ Without the teachings and concepts espoused by Dr. Deming, lean most likely would not have caught on as early and with as much enthusiastic support as it did here in the United States.
THE UNIVERSAL APPLICABILITY OF LEAN
Although Lean is able to be applied to the process that Ford used in the United States nearly 100 years ago at his plant in Highland Park, Illinois, the concepts were not actually honed and applied until Honda and Toyota caught on to the value of these ideas (thanks in no small part to the aforementioned Dr. Deming). The Japanese formulated a core tenet of lean — Just In Time (JIT) — which proved to be a concept with long-lasting impact.
LEAN TODAY
For the present-day, lean is still regarded as essential for auto manufacturing. In addition, the core philosophies have been introduced into the fields of health care and computer programming. As a matter of fact, lean’s popularity in these two fields has been deemed to be growing “rapidly in popularity.”
Leave a Reply