Your cart is currently empty!
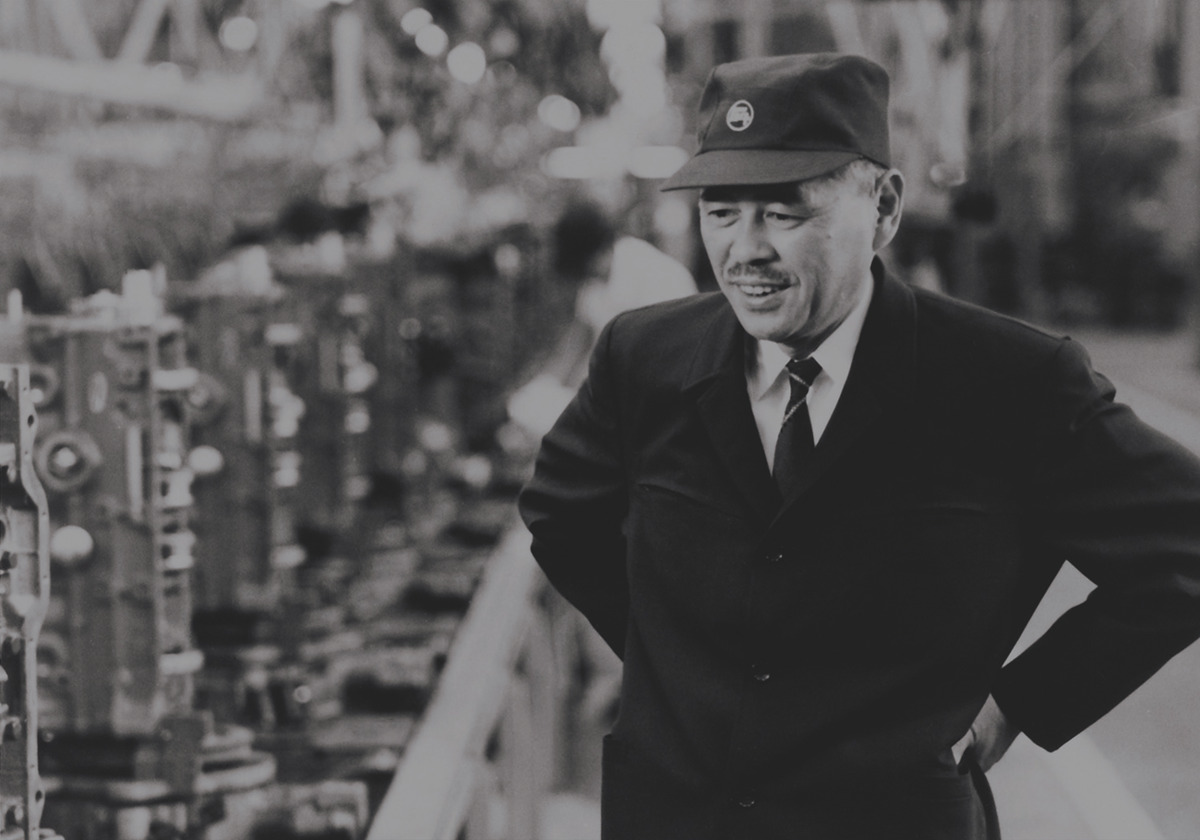
The 8 Types of Waste in Lean
What is Lean?
Lean’s origins date back to the post-WW II era in Japan. It was developed by Taiichi Ohno, a Toyota production executive, in response to a number of problems that plagued Japanese industry. In fact, what we now refer to as “Lean” is based on the Toyota Production System. The main problem facing Toyota was that the domestic Japanese market didn’t need large numbers of identical cars or trucks. Smaller quantities and a lot of variety were the order of the day. Mass production techniques, which were developed by Henry Ford to economically produce long runs of nearly identical products, were ill-suited to the situation faced by Toyota. Today the conditions faced by Toyota in the late 1940s are common and Lean has been adopted by businesses all over the world as a way to improve efficiency and to serve customers better.
A major focus of Lean is the ability to rapidly and automatically reconfigure organizations in response to changing needs of the market. Flexibility is the key. This flexibility is possible only if waste is systematically targeted and eliminated. Waste, called Muda in Japanese, comes from a variety of sources. It takes training in the Lean approach to see waste in an operation. By the way, the word Lean was not used by Toyota. It was coined by American researchers who studied the Toyota approach in the 1990s.
8 Types of Waste
Lean is all about eliminating waste in value streams. To accomplish this goal you must identify waste. This task is easier if you have more detailed knowledge about what kind of waste to look for. Then you can address the more manageable waste categories, rather than tackling all types of waste at one time. This exercise will help you develop skill in identifying waste by telling you about useful waste categories.
OVER-PROCESSING
Over-processing is processing things that the customer does not want or is unwilling to pay for. This type of waste includes things like over-processing of parts due to poor tool and product design, asking the customer for the same information multiple times, or giving the customer information that they don’t need or can’t use.
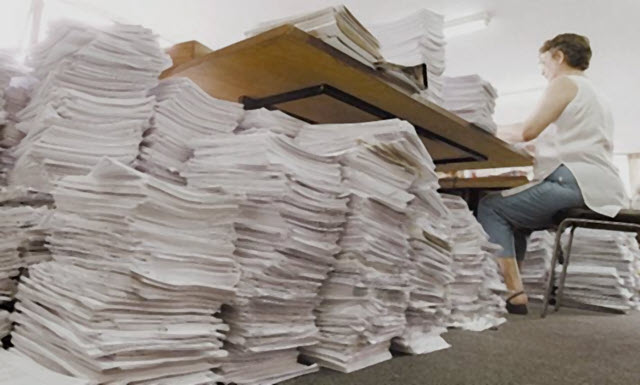
TRANSPORT
Transport waste results when you move information or things farther than necessary. This includes such things as temporarily storing, filing or stocking. Although transportation sometimes can’t be avoided, it doesn’t add value and should be minimized.
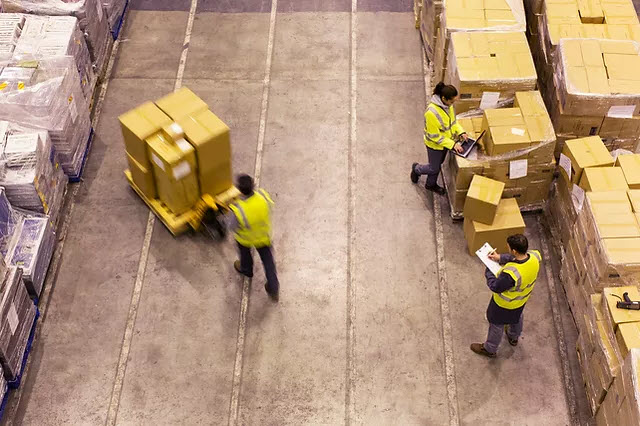
WAITING
Waiting, or idle time that causes the workflow to stop, is wasted time.
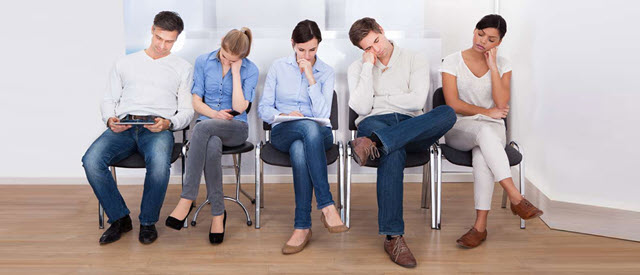
OVER- OVERPRODUCING
Overproducing means producing too much of something, or producing something before it is needed. This includes manufacturing units, or in an office environment, unnecessary paperwork or information. With Lean, we try to make what is needed at the time that it is needed.
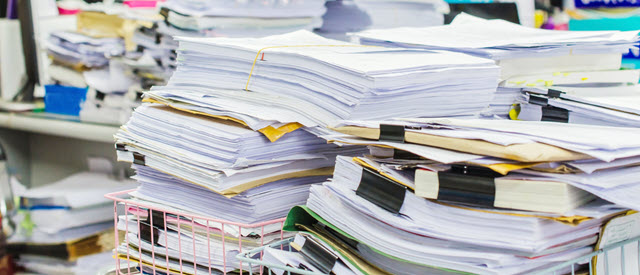
INVENTORY
Inventories is having more than the absolute minimum needed to do the job. For example, unneeded supplies, paperwork, copies, or holding an item longer than necessary. A buyer holding a purchase order longer than necessary is an example of work-in-process inventory, and it is waste! Inventory is related to overproducing. However, overproducing creates the inventory in-house, while inventory also includes supplies you purchase.
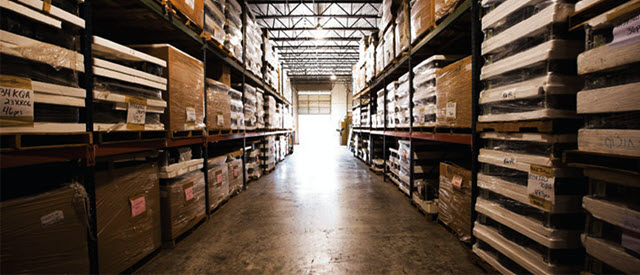
UNNECESSARY MOTION
Unnecessary movement by employees during the course of their work, such as looking for parts, tools, prints, help, etc. Think of processes that have people and things moving much more than they need to.
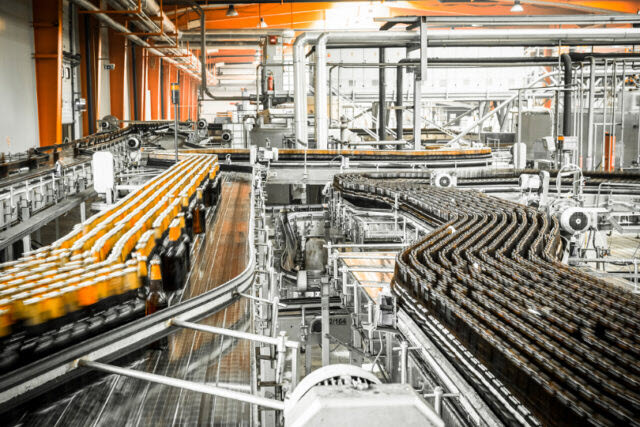
DEFECTS
Producing work that results in product or service that does not meet the customer’s requirements and requires re-work or scrap is waste due to defects.
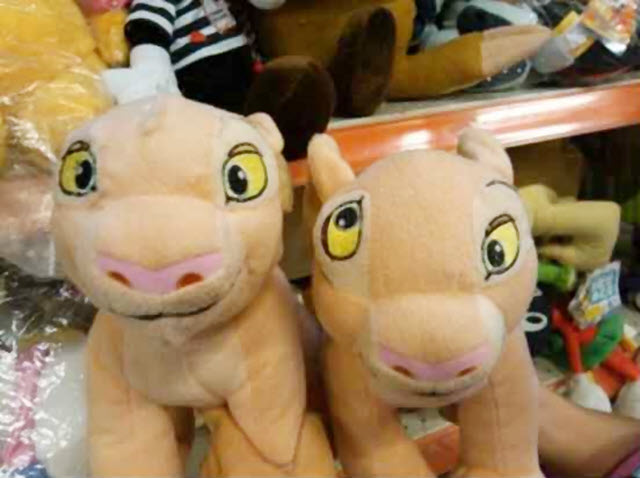
WASTED HUMAN POTENTIAL
Perhaps the saddest waste is when skilled people are not utilized to the fullest. Their contributions are restricted, their ideas ignored, and their skills are underutilized. Lean is all about maximizing the contributions of everyone in the organization.

Keep in mind that this is not a comprehensive list of waste, there is no such thing. Learn to ask if what is being done adds value and if it doesn’t, think about ways to reduce or eliminate it. Lean is a journey of continuous improvement.
What other types of waste can you think of? Let me know in the comments.
5 responses to “The 8 Types of Waste in Lean”
-
Control charts are the foundation of Continuous Improvement, so I’d add #9 as:
1) Over-processing
2) Transport
3) Waiting
4) Over-production
5) Inventory
6) Unnecessary motion
7) Defects
8) Wasted human potential
9) Not Listening (to the Voice of the Process)-
I love to read that the adding of “not listening (to the Voice of the Process)” is one type of the waste.
In my experiences, I saw that people tried to improve a process but its control chart showed the process was not stable and predictable. So, they just waste time and efforts to improve the unknown and noises on their process.
-
Agreed Canh, if a process isn’t stable and predictable according to an IMR or XBarR control chart, then the first order of business is to identify the cause of assignable cause variation and take remedial action.
-
-
-
Here’s a tenth:
1) Over-processing
2) Transport
3) Waiting
4) Over-production
5) Inventory
6) Unnecessary motion
7) Defects
8) Wasted human potential
9) Not Listening (to the Voice of the Process)
10) Not Listening to TaguchiToo often, people think in terms of PASS and FAIL. Taguchi argues quite convincingly that if your off target, you’re losing money, even if you’re “In spec”.
-
Thanks for mentioning the term of PASS and FAIL Steve.
Taguchi invented the loss function concept explaining that merely attempting to produce a product within specifications doesn’t prevent loss!
The PASS and FAIL mindset for me is just a narrow look of individual results and ignore the look of the process as a whole where we can study and make the improvement and save cost.
-
Leave a Reply