Your cart is currently empty!
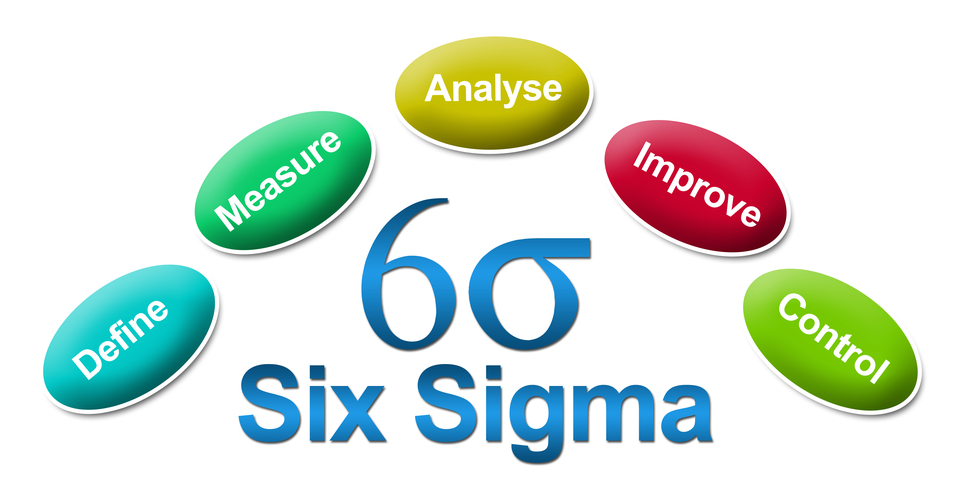
A Few Words About Six Sigma
What exactly IS “Six Sigma” and what can it do for my organization? Succinctly stated, Six Sigma is a data-driven procedure through which problematic issues in any process (e.g., manufacturing, product delivery, service transactions, etc.) can be significantly reduced, if not totally eliminated.
Introduced in 1986 (trademarked in 1993) by Motorola engineers Bill Smith and Mikel Harry, Six Sigma was later (1995) adopted as a primary business strategy by General Electric CEO Jack Welch and has since permeated multiple industrial sectors throughout the world.
The term itself is derived from the sigma rating (i.e., percentage of defect-free products) of a matured manufacturing process and the statistical measure of six standard deviations from the average. Motorola’s self-imposed goal of “six sigma” (i.e., 3.4 defects per million outputs) established (and subsequently served to perpetuate) the generic title by which the process of quality improvement has come to be known.
The ultimate quality of the output of a process can be significantly improved through definitive Six Sigma procedures. Essentially, a specified set of quality management methods utilizes empirical, statistical analysis to identify causes of problems and subsequently enables efforts to reduce, if not indeed eliminate, these issues. Through minimization of statistical variability in the processes associated with manufacturing and/or business endeavors, personnel trained in Six Sigma specify value targets to be achieved. Examples of such focuses include the reduction of costs, pollution, process cycle time, etc., as well as the measurable enhancement of customer satisfaction, employee retention, etc.
Six Sigma objectives are accomplished via the direct implementation of either of two sub-methodologies: DMAIC and DMADV. Through defining, measuring, analyzing, improving, and controlling, personnel trained in the principles of Six Sigma are able to imbue existent organizational systems with the adjustments deemed necessary to facilitate gradual, incremental improvement. Similarly, for the development of new processes or products that will satisfy the optimal standards inherent in Six Sigma, the phased efforts of defining, measuring, analyzing, designing, and verifying will be applied.
A 2002 derivative of Six Sigma is Lean Six Sigma. This approach is characterized by direct elimination of “muda,” or the waste that occurs in relation to eight facets of manufacturing and/or business. Key elements of time, inventory, motion, waiting, over-production, over-processing, defects, and skills (acronym: TIMWOODS) are targeted to be made “lean.” This focus on waste elimination, in conjunction with the Six Sigma reduction of defects and critical to quality (CTQ) characteristics, serves to foster a more efficient and effective operation, thus saving time, effort, and money.
So what? While it all sounds well and good to try to improve upon any given organizational process, why should anyone invest specifically in Six Sigma training? Well, how about to save a lot of money!? It is estimated that Six Sigma experts (i.e., “black belts”) save companies approximately $230,000 per project. It is noted that the United States Army ($2 billion), General Electric ($1.8 billion), Ford Motor Company ($1 billion), and Allied Signal ($800 million) claimed substantial benefits directly attributable to their Six Sigma utilization (Monk, 2015). It was also reported by the American Society for Quality (ASQ) that an independent study found that “ … effective implementation of Six Sigma led to an average savings of 1.7 percent of revenues over the period of implementation and an average return of more than $2 in direct savings for every dollar invested on Six Sigma” (Pulakanam, 2012). Thus, the reported return on investment (ROI) in Six Sigma was more than 100%.
It would thus seem that an investment in Six Sigma would constitute an intelligent move if the objective of achieving significant improvement in efficiency is desired. Please visit our website or contact us via the link below for a more complete provision of information about the value and benefits of Six Sigma.
If you are interested in Six Sigma Certification and Training, contact Pyzdek Institute today!
References
Monk, J. (2015). Saving from the start with Lean Six Sigma. Six Sigma Daily (15 February 2015).
Pulakanam, V. (2012). Cost and savings of Six Sigma programs: An empirical study. Quality Management Journal, October 2012, vol. 19 no. 4, pp. 39-54.
Leave a Reply