Your cart is currently empty!
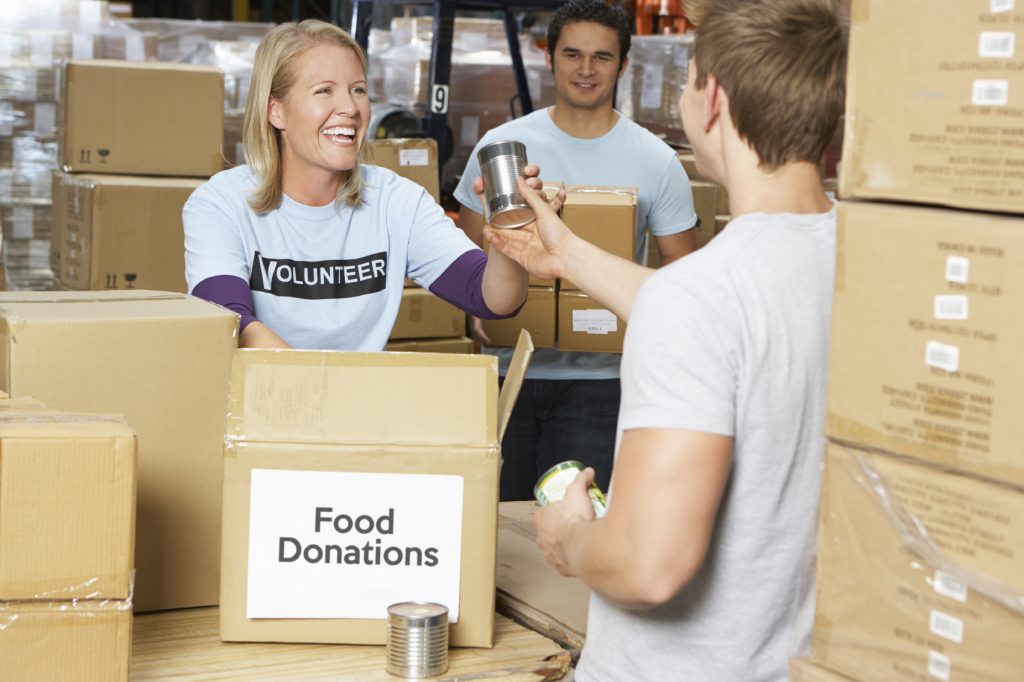
How Six Sigma Training Is Helping Nonprofits
Six Sigma training has been successfully used to improve corporate operations for decades, and now some nonprofits are discovering that the principles can help their organizations streamline the way they run things as well.
Crain’s Business Cleveland reports that a food bank in Ohio, the Akron-Canton Regional Foodbank, was able to cut the number of days it took to receive, sort, inspect, pack and deliver food donations by 40 percent, from an average of 92 days to 39 days, after receiving Lean Six Sigma training. The nonprofit wants to cut that number of days down even further and believes they can achieve that goal.
โWeโve only been doing this project since the end of December, so I think the more we get more people involved in this, I think that 39 days โฆ could be in the 20s,โ said Matt Petrick, senior manager of operations for the food bank.
The benefits to the food bank are obvious. According to the Crain’s article, the food bank’s volunteer center would hold up to 180,000 pounds of food donations at a go, which could take up to three months to distribute. This long period meant that foods could expire easily and volunteers would have to re-inspect donations on a regular basis. Now that storage time has been cut down significantly, re-inspections no longer have to take place. In addition, by getting donations out of the door more quickly, only 60,000 pounds of food, a third of what it was previously, is stored at the food bank at any given time.
An important side benefit, especially for a nonprofit that depends on volunteers, is that the volunteers now have more time to get to know one another and thus build up a greater sense of teamwork.
Leave a Reply