Your cart is currently empty!
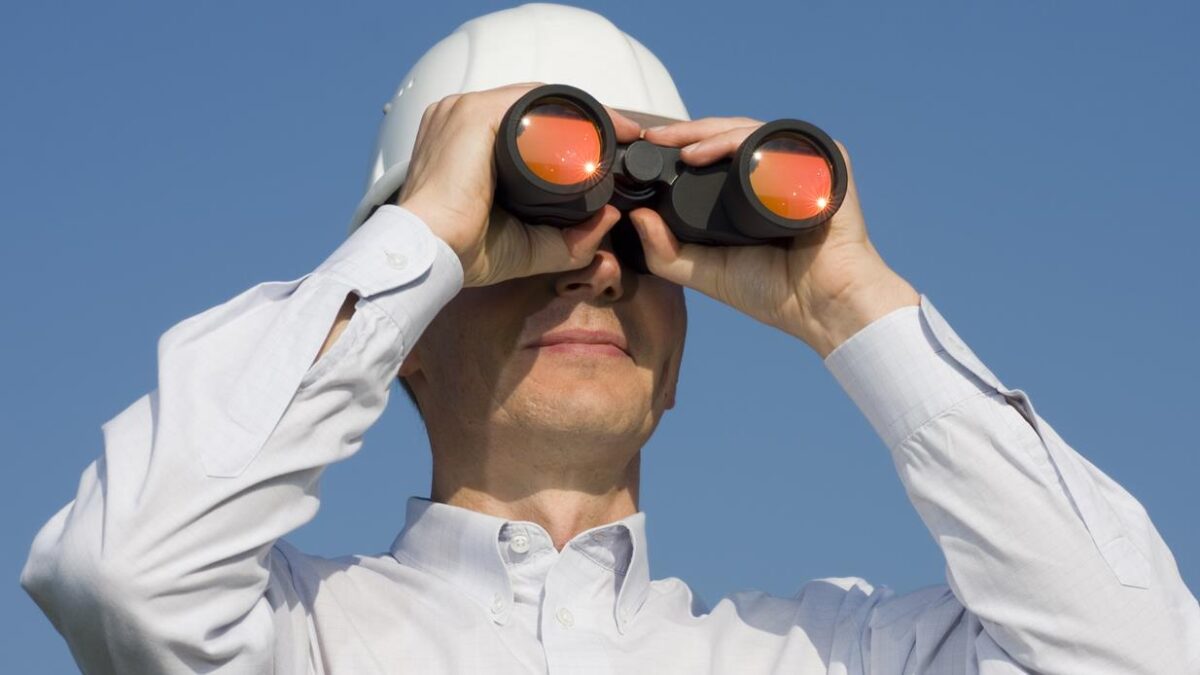
Recognizing a Six Sigma Project Opportunity
Lean Six Sigma projects must help the organization achieve its goals. To accomplish this you must take action that guarantees that your project activities are directly linked to the goals specified by your leaders.
Example of a CEOโs Vision
Six Sigma begins with the vision of the senior leader and his or her team. The organizationโs CEO has the difficult challenge of balancing short and long-term goals and balancing goals for different stakeholders.
Examples of goals for customers might include increasing the number of profitable customers or increasing the number and percentage of customers who are net promoters. For employees, the CEO might look at making employees feel like they are part of a high performing organization, increasing employee satisfaction on surveys, becoming the employer of choice in their area, or becoming a recognized leader in developing employees. For shareholders, the CEO might have specific numerical targets, such as earnings per share or price-earnings ratios, or he may target a qualitative goal such as consistent growth and performance.
Customer Goals | Employees Goals | Shareholders Goals |
---|---|---|
|
|
|
The Yโs Are the Objectives
To achieve our objectives, we must determine what we need to do. This process begins by thinking of our goals as an end result that is driven by a number of causes. In Six Sigma we say that we are โsolving forโ the end result, which we call Y. In high school math you are taught that Y can be modeled as an answer that depends on some other variables, which your math instructor referred to using one or more terms identified with the letter X. The equation that shows the relationship between the Xs and the Y is called a โtransfer functionโ in Six Sigma.
Y=Function\ of\ (x_{1},x_{2},\ldots, x_{n})
Itโs usually not mathematical, at least not early in your project. Still, itโs a helpful way of thinking about goals. You need to think about the Ys your leaders are considering for customers, shareholders, and employees. There will be Xs for customers, for shareholders, and for employees. Identify which Xs need to be improved to reach each Y. Also, think about how you will measure each X and Y, if your leaders havenโt thought of this already.
Customer | Employee | Shareholder |
---|---|---|
Y: Wow customers | Y: Revenue and proforma EPS and OP income growth | Y: Great place to work & high performance organization |
Xs: ? | Xs: ? | Xs: ? |
Measurement tools: ? | Measurement tools: ? | Measurement tools: ? |
Planning What We Need to Accomplish
It is helpful if you think of the process of defining a suitable project as a โdrill downโ process. Start with the objectives for each stakeholder. These are your corporate Ys. Then determine how each Y might be measured. These metrics are called critical to quality, or CTQs, because they will determine how well the higher-level Ys are accomplished.
Now go down another level to plans and projects that can make the CTQ metric move in the desired direction. At some level, you will be able to identify a Six Sigma project candidate that you could undertake as a Black Belt to help your organization achieve one or more of its Ys. By using this process, you will know precisely how your activity links to the vision of your senior leadership. And this is called a โline of sightโ for your project.
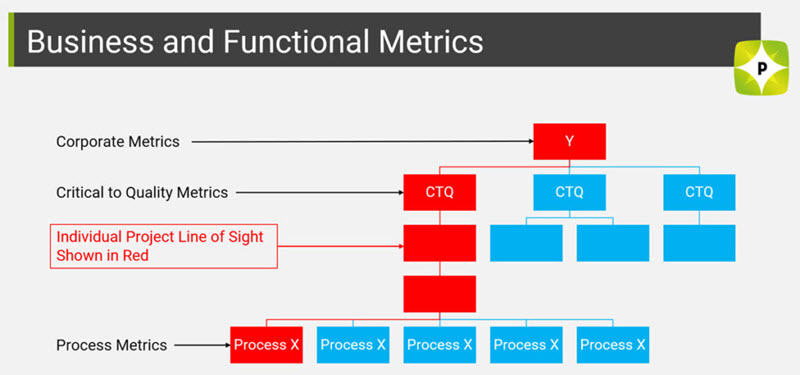
Overview of Goal Flow-Down
Letโs take a look at the overall process. It all starts with external stakeholders, customers and investors. The CEO will choose a result, a Y, to meet a stakeholder demand and will identify several drivers, or Xs, that will have an impact on the Y. Each X will become a Y that the next lower level of management will work to improve.
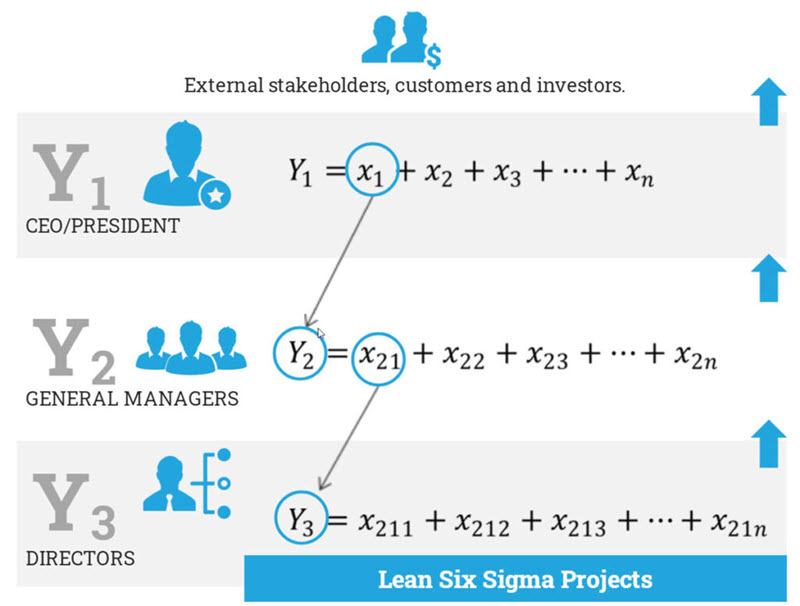
This process will continue until it reaches a level where a Six Sigma project can be chartered to drill all the way down to root causes. These projects will improve the root causes, and the results will flow back upwards to the top-level goal.
One response to “Recognizing a Six Sigma Project Opportunity”
-
This is a great overview of the importance of linking process improvement tasks and other work to overall corporate goals.
I’d add that it’s critical for the C-level people that set the corporate direction and priorities get out of their offices and visit the people doing the actual work (Production, Supply Chain, Planning, Process Engineering, etc) and ask what they (C-Levels) can do to help. If they visit the workplace and cajole, monitor or criticize, they’ll end up with just the opposite of the desired effect
Leave a Reply