Your cart is currently empty!
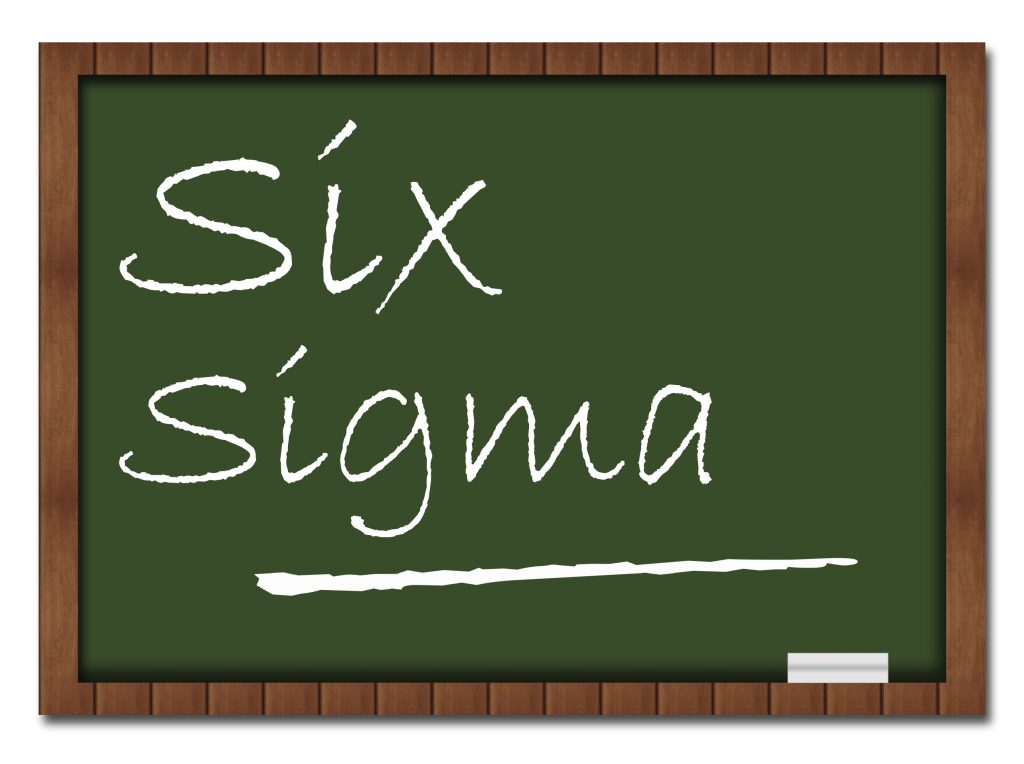
Six Sigma vs. Lean Six Sigma: The Similarities and Differences
All businesses are interested in streamlining their processes and eliminating waste, but not all companies agree about the best way to accomplish that goal. Six Sigma is one popular way to do it. There is also Lean Six Sigma, a modified version that has the same goal. In this blog, we’ll look at Six Sigma vs. Lean to help you understand the difference between the two approaches.
Six Sigma
Six Sigma aims to improve quality and efficiency by eliminating defects and waste. It looks to achieve that goal by streamlining and improving business processes across the company, from customer support to manufacturing and service delivery. Implementing the process on a wide scale can help an organization achieve measurable results.
Lean
In Lean, the emphasis is on eliminating wasteful steps unnecessary and wasteful steps in a product’s creation, leaving only steps that add direct value to the product. The customer-focused Lean approach determines what is essential by considering whether a customer would pay for it. Taking out wasteful steps leads to a streamlined and profitable manufacturing process.
The main difference between the two approaches is that Six Sigma proponents believe that variation in the process leads to waste, while Lean practitioners believe that unnecessary steps in the production process, which don’t add value to the finished product, lead to waste.
At the Pyzdek Institute, we offer accredited Six Sigma and Lean Six Sigma training and certification.
Leave a Reply