Your cart is currently empty!
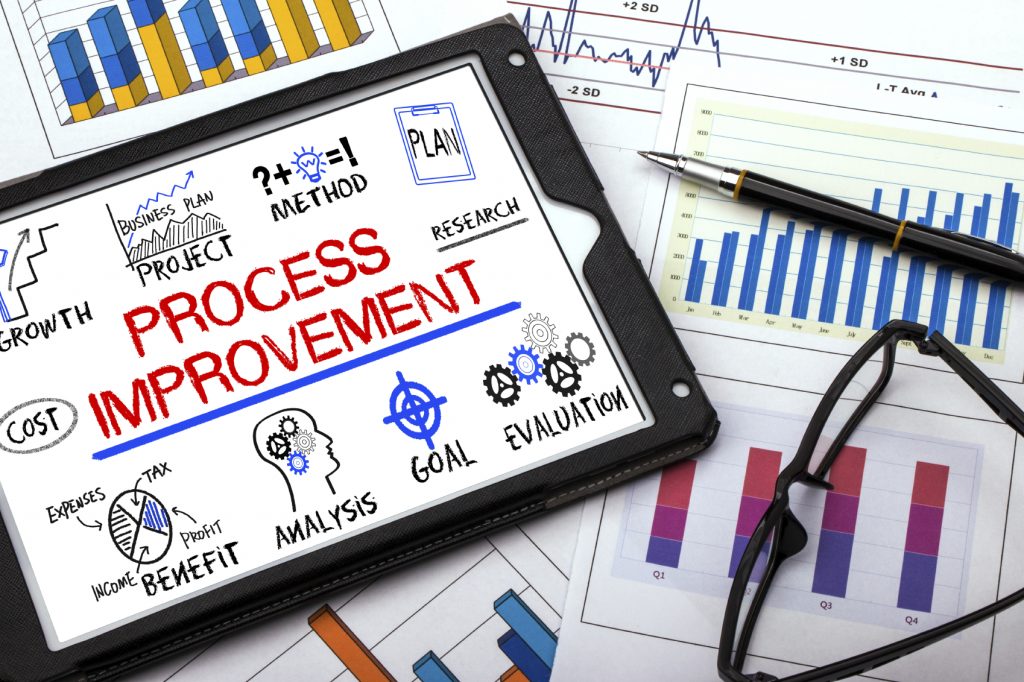
Why Six Sigma Training Is Necessary To Improve Your Business Processes
Six Sigma experts are now being sought after by big companies because of the inestimable benefits their business will get from Six Sigma. While the benefits are infinite, the major ones are easily highlighted.
Reduction of All Forms of Waste
Cutting process activities down to the necessary ones reduces the amount of time or resources wasted on a daily basis. This will lead to improved productivity as the resources saved can be invested into some other business activities. This benefit applies to almost any kind of resource used in business. Streamlining resource usage can increase productivity dramatically without the need to add more resources.
Improved Competitiveness
The impression your company gives customers starts from the back end. Front line employees only reflect what happens within. So, when your business activities have been fine-tuned, shortened and better positioned with faster results, it will result in improved customer experiences and thereby earn you more customers. Every customer likes speed and accuracy. Six Sigma will facilitate a shorter turnaround time. Six Sigma has a way of identifying and standardizing common comments among customer feedback that can improve customer experience over time if properly taken into account.
Improved Supply Chain Management
One of the major objectives of Six Sigma is to reduce the defect rate to about 3.4 in every million. So, if the principles of Six Sigma are followed strictly in the supply activities of your company, your defect rate will be reduced to a minimum and this will help increase your bottom line.
Improved Productivity
Since all forms of waste will be eliminated, the resources will be applied judiciously and that leads to increased productivity.
In summary, Six Sigma training helps to plug all forms of waste and leakages by streamlining business activities to achieve maximum output.
Leave a Reply