Your cart is currently empty!
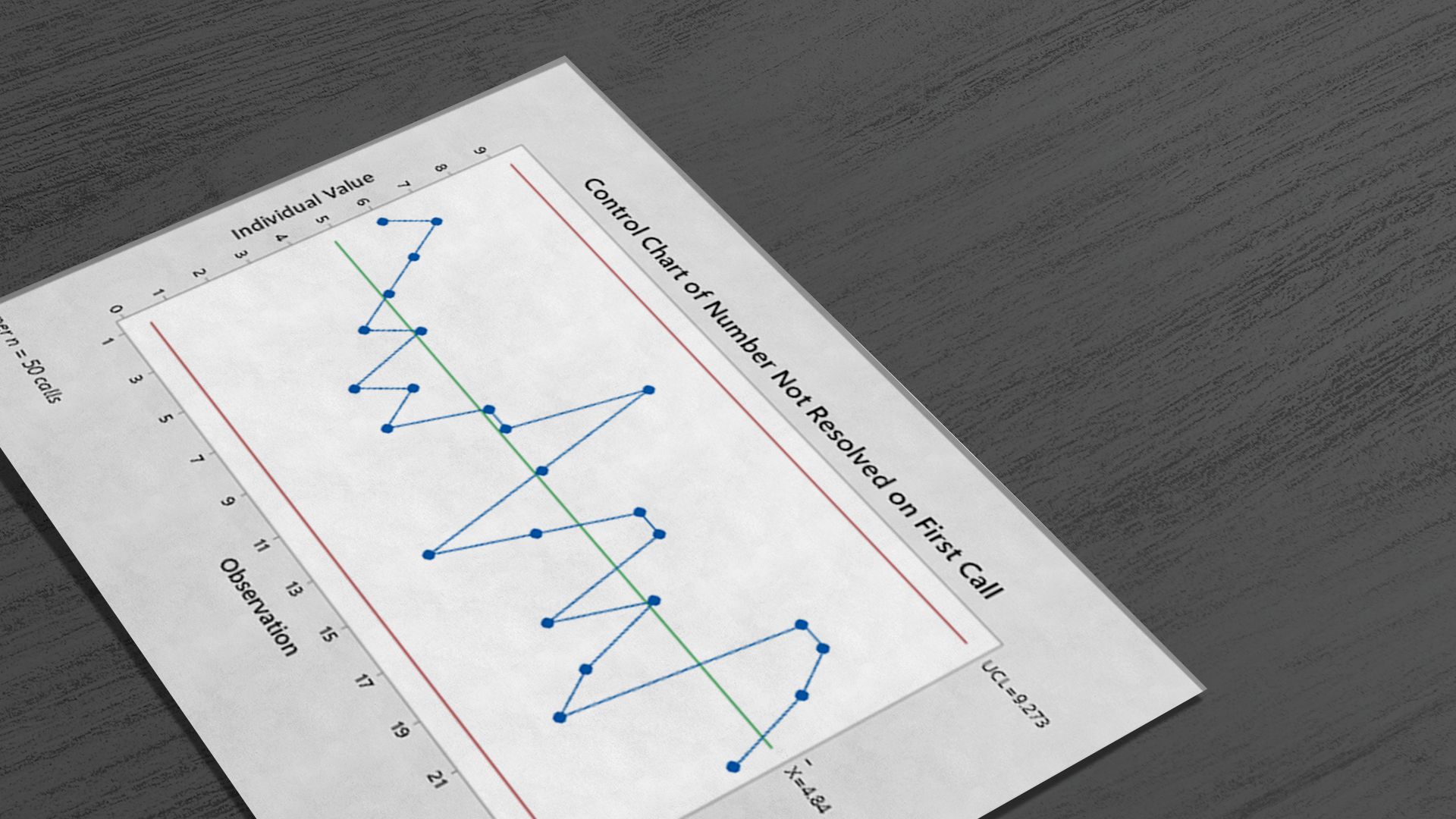
Let’s Return to Simple
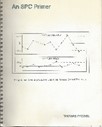
I recently re-read my original book An SPC Primer originally published in 1978. It brought back my early days in process excellence. At the time I was the only quality control person in a factory that covered an area of 1 mile plus. I was working the graveyard shift and my task was twofold.
- Visit as many running process areas and machines as possible.
- Respond to emergencies.
As you might imagine this made my work day rather hectic. At the time I had just discovered a man who later became my mentor, Dr. W. Edwards Deming. Dr. Deming was the man who taught quality and process control to post-war Japan. While he was a famous man in Japan, he was for the most part unknown in his home country of the USA. The Japanese, learning from Deming, made quality everyone’s job. I decided to do the same and started teaching supervisors and factory workers to monitor the quality of their own work. Central to this was SPC, statistical process control. More specifically, control charts.
The SPC primer presented a programmed learning approach to statistics and control charts. Readers were actively lead through elementary arithmetic and the creation of simple control charts. I used the primer to train factory personnel to track their own work. When the control chart showed a problem, workers looked for the cause, which they usually found quite readily. If not they notified their supervisors. The supervisors demanded that I train them in SPC too so they understood what their employees showed them. If they couldn’t find the problem I was called. If I couldn’t find the problem the supervisor stopped the process and I left the day shift quality engineers a copy of the control chart and an explanation of the investigations already done on the graveyard shift. Soon my workdays were much less chaotic. More important, quality soared to new levels of excellence.
The morale of the supervisors and workers on the graveyard shift went from the worst to the best. Much was learned that was incorporated into work standards and blueprints.
All of this was accomplished with Six Sigma Black Belts, which wasn’t to appear for many years. Quality levels and productivity improved. In short, simple worked!
2 responses to “Let’s Return to Simple”
-
This is a great message. What I find particularly interesting is that when the individual operators were able to track and make improvements to their processes, moral and productivity improved. In short when there was improved ability for feedback to the operators on their efforts and adjustments were able to be made, the whole culture of the organization was given a significant boost.
If only more bosses, would see that by simply by giving more feedback at an individual level, it clarifies expectations, helps to improve communication and overall business results.
-
Yes, the improved employee morale is a big plus. Why let all that brainpower go to waste?
-
Leave a Reply