Your cart is currently empty!
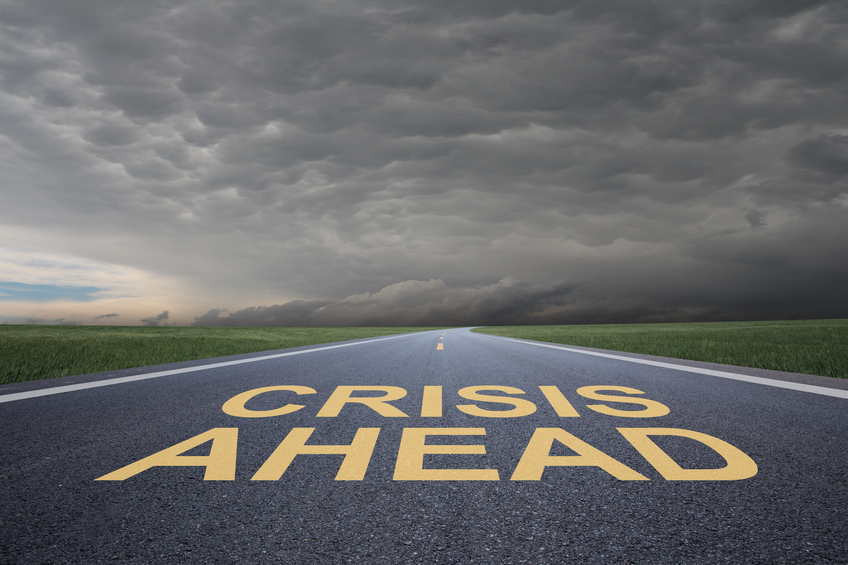
Tips for Avoiding the Top 10 Nightmare Equipment Failures
You’re worried about costs, sales, planning, and deadlines. You don’t even think about the possibility of a major equipment failure until it happens. Just one instance of a boiler breakdown, turbine malfunction, or generator outage can cost your organization millions of dollars and lengthy downtime, to say nothing of your reputation taking a hit and causing a drop in shareholder value and market share.
FM Global, one of the largest industrial and commercial insurers in the world, explains ten of the most costly equipment failures and what you can do to prevent them.
Transformers
Transformers distribute power throughout the property. When one malfunctions and a blackout ensues, the most common cause is a breakdown of the paper insulation surrounding the internal copper wires. The loss of a transformer can cost a business up to $10 million and two full years of downtime. You can avoid this by sampling the insulating oil on a regular basis.
Boilers
These create steam that’s used to produce electricity or some similar industrial process. A boiler breakdown typically involves a failure of the internal tubes carrying the water. Not quite as pricey as a broken transformer, but it can still cost upwards of $2 million and weeks of downtime to repair. Monitoring the water chemistry for rust-causing sulfites and other solid buildups can warn you ahead of time.
Switchgears
This includes elements such as fuses, circuit breakers, and switches that support distribution of power throughout the building. Sometimes the mechanical components will bind together, which leads to electrical arcing and – if left unchecked – a fire or explosion. Anything connected to them might also be damaged. This can lead to hundreds of thousands of dollars in repairs (millions, if a fire breaks out). So keep the environment dry, clean, and clutter-free.
Chemical Vessels
These do just what it sounds like – they hold chemicals while they’re mixed for the market. Most often, you’ll find cracks somewhere in the equipment that create leaks and pricey cleanup – $1 to $2 million, if there’s been no explosion yet. Keep an eye on the vessel welds through regular inspections to avoid this.
Turbines
Turbines keep the electricity generators moving by utilizing steam, water, gas, or wind. Design defects, excessive vibration, and foreign objects can cause blade failure that leads to the turbine seizing up and becoming damaged. This will cost your business up to $60 million and 18 months of downtime. Regular inspections of the blade roots (where the blades attach to the shaft) can help prevent this.
Compressors
These create pressurized air for practically any industry. Too much vibration can lead to equipment failure and costly damage to the pipework and bearings. This one will really hurt your business financially – up to $120 million. Periodic checks or vibration monitoring equipment will help you keep track of this, and you should also watch for unbalanced mounts, a bent crankshaft, loose belts and bolts, and a misaligned flywheel or pulleys.
Human Error
Perhaps the most common cause of equipment failure, an operator will occasionally press a wrong button or try to cut corners. Depending on what they break, the repair can be a cheap one or cost millions of dollars. Remember to offer refresher and emergency training often to keep them up to speed.
Generators
This equipment converts the rotational energy from turbines into electricity. The insulation protecting the windings can fail and create permanent damage. Replacing a generator can cost up to $60 million and 18 months of downtime. So don’t forget to regularly maintain and inspect them.
Planned Outages
Sometimes you just have to shut things down to fix them. Occasionally a worker will forget some tools inside the equipment that will ruin it when it’s turned back on. This can cost the business up to $60 million and many months of downtime. Formally keeping track of tools in the work area (for example, a sign in/out log) can help prevent this.
Molten Material Production
Some businesses use this method to transform raw materials into alloys. A power failure can cause that metal to solidify inside the machinery. Cleanup can cost upwards of $80 million and months of downtime. So remember to ensure the integrity of the electrical service to this equipment.
Leave a Reply