Your cart is currently empty!
Lean Six Sigma Improvement and Work Design, Part 4
This is the fourth post in a series taken from a lesson in Pyzdek Institute Lean Six Sigma Black Belt training. Future posts will continue the topic. You can find all of the articles in the series by searching this site for the title.
What methods should be used to accomplish the goal using the resources (materials, machines, and manpower) that we have?
What standard work procedures should everyone follow? (Standard Operations Routine Sheet)
Designing continuous flow work cells involves developing standard operations. These are descriptions of work that combine people, equipment and materials to create value as effectively as possible. The components of standard operations are takt time, the work procedure, and the parts and materials essential to start work within the process, including parts or materials at the machines. If all three of these components are not present, standard operations cannot exist.
At companies like Toyota standard operations are determined by the foreman. Toyota foremen are masters of the work being done by their employees. Foremen are able to demonstrate the standards to their people. If an impartial observer agrees that the pace of work being done by the foreman following the standard is appropriate, then Toyota expects workers to adhere to the standards.
In many companies, however, things are done differently. It is my experience that there are few foremen who are able to do all of the work being done by their employees. The history of management in America and most European countries has led to a system where work is designed by experts in work design (industrial engineers,) supervised by experts in management (foremen and supervisors,) and performed by blue-collar specialists at a given trade (machinists, assemblers, welders, assembly line workers, etc.). This model worked adequately[1] in the past for batch-and-queue systems where specialization was the norm, but it is no longer possible to remain competitive using this approach.
However it raises a question: if we donโt have a well-rounded supervisor to design work, how can it be done? The answer arrived at by many companies is to use teams. Teams designing and analyzing work are provided with basic training in the principles of work design, inventory control, and lean; thatโs what this lesson and previous lessons are all about. The team must include at least one member who is highly skilled at the work done at each process in the subproject loop. Preferably this will be the same person, but if there is no such person available the team may have more than one skilled worker. Once the work of several people/machines is combined into a work cell, the company will need to cross train all of the workers in the cell so that they may help one another.
It may be that no one person on the team knows as much about work design as the industrial engineer, or as much about management as the business school graduate, or as much about any operation as the blue-collar journeyman, but experience has shown that tremendous improvements are possible using the team approachโif the company leadership truly embraces the Lean philosophy.
Standard operations are the sum total of all of the ways that people, materials, equipment, and information combine to create value. There are three components to standard operations:[2]
- Cycle time
- Work procedure (work sequence)
- Standard stock on hand (WIP)
Each of these items is required to standardize the operations.
Are there any โtipsโ that people should know about doing the work?
Knowledge of work is often a collection of insights. Experienced people have developed tricks that make it easy to do the task at hand, or help them avoid problems that might causes injuries or quality issues. When designing the work you should create a document that can be given to workers showing them what to look for. This will include such things as the work sequence, how to handle the items, how to set up the tools needed for the job, and other relevant work details. The emphasis is on specific, concrete directions. Avoid abstractions. Include drawings, videos, pictures, animations, and other media to help show the proper way to do the work. Flowcharts are often helpful.
A good model for work instructions are the instructions provided to customers for assembling products. Figure 1 shows the instructions for assembling a babyโs crib. It includes step-by-step directions, drawings, safety warnings, tips on how to put the crib together more easily. It also includes tips on maintenance, cleaning, and storage; guidance on how to test your work to assure that itโs done correctly; instructions on changing the crib into a toddler bed; etc.. Think of work instructions as the workplace counterpart to assembly instructions for consumers and youโll have a good idea of whatโs needed. The idea is to provide simple, easy-to-understand, and complete instructions.
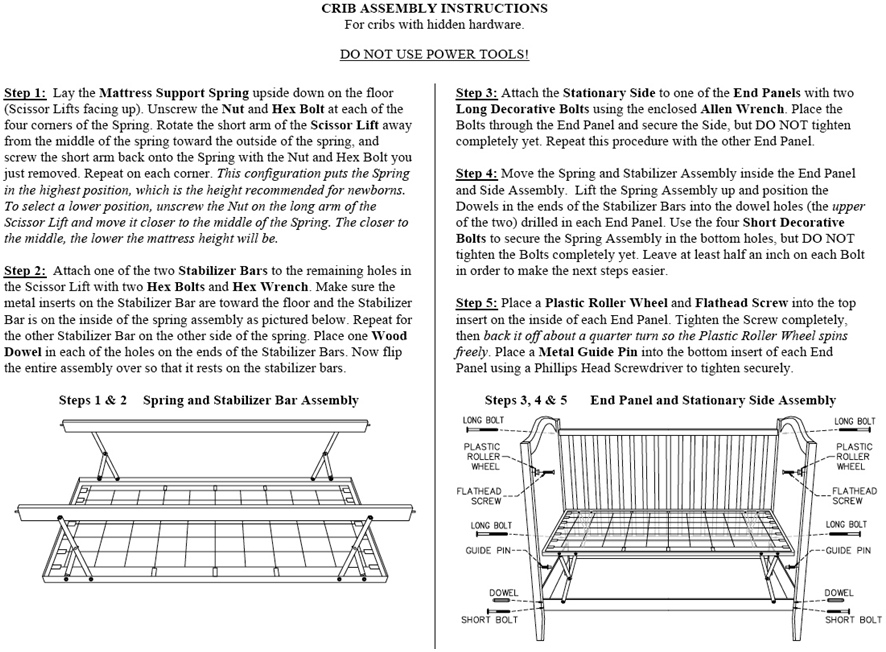
Manual of Work Directions
The manual of work directions tells how to perform the standard operations properly. It is based on the production capacity table (e.g., Figure 1 in an earlier post) and the standard operations routine sheet. It describes the work to be done by each person in the work cell. In addition, the manual includes:
- Safety and quality items for each step in the work sequence;
- Illustrations of machine placement for work performed by each individual worker;
- Cycle time for each operation;
- Work sequence;
- Standard stock on hand;
- Instructions for checking quality.
Machine placement is shown on a separate sheet of 11×17 paper (A3 paper.) The sheet will have columns showing work sequence, standard stock on hand, cycle time, net operating time, and safety and quality checks. The completed sheet is called a Standard Operations Bulletin (see Figure 2.) Standard Operations Bulletins are displayed at the line and show the workers what is expected of them. In addition, supervisors can use the bulletins as visual control tools to audit compliance with work instructions. Managers and Process Improvement Teams can study the bulletins for ideas on improving the work.
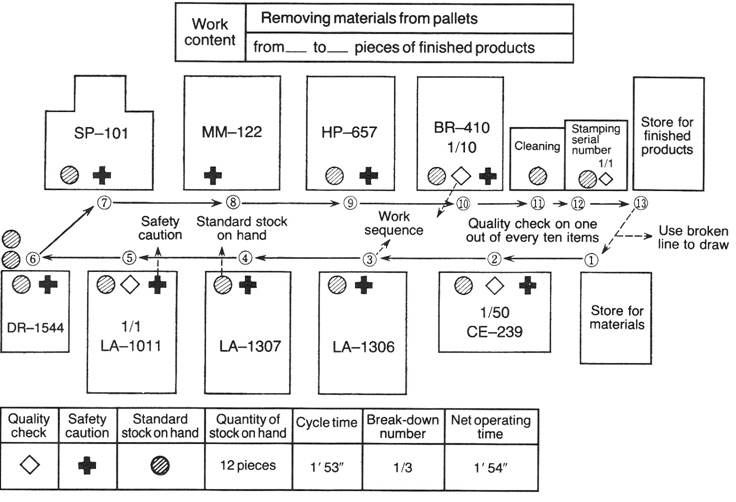
[1] This is a debatable premise today, but it isnโt fair to judge past behaviors by current day standards.
[2] Kanban Just-in-Time at Toyota, 1989, Lu, David J. translator, Productivity Inc., Portland, OR., p. 101.
[3] Kanban Just-in-Time at Toyota (1989), Productivity Press, Portland, OR. P. 114.
Leave a Reply