Your cart is currently empty!
Lean Six Sigma Improvement and Work Design, Part 7
This is the seventh post in a series taken from a lesson in Pyzdek Institute Lean Six Sigma Black Belt training. Future posts will continue the topic. You can find all of the articles in the series by searching this site for the title.
How many people are needed?
Consider the process described in Figure 1 in part 3 of these series. The requirement for this process is shown in the figure to be 255 units. The teamโs idea for the process was to set it up as shown in Figure 1. The U shape will minimize the distance that people need to move. Figure 2 shows the standard operations routine sheet for the process. This sheet graphically shows a time line for each operation, the manual time, the automated machine time, and the travel time. The total time to complete a full cycle for this process is 113 seconds (see either Figure 2 or Table 1.) Although some machines continue to operate automatically at this time, the operator can return to the beginning of the process and start another cycle. By the time the operator reaches each operation on the next cycle, the machines will have completed their cycle and, due to autonomation (Jidoka) they will have automatically stopped.
This process can be operated by one person. A full dayโs production can be produced from this process in 28815 seconds. Since a full work day is 51600 seconds, the worker will have time to perform other duties each day, including 5S (see below).
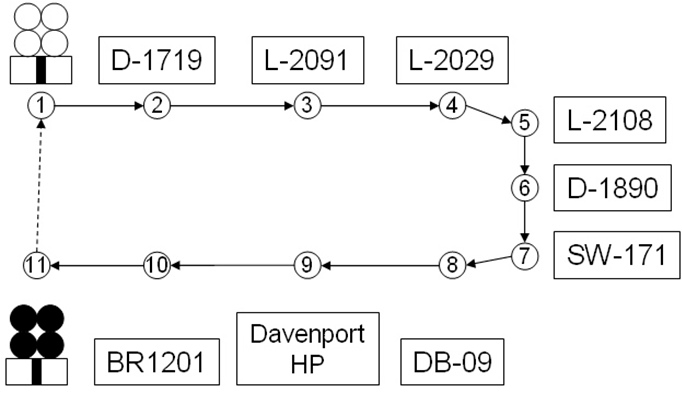
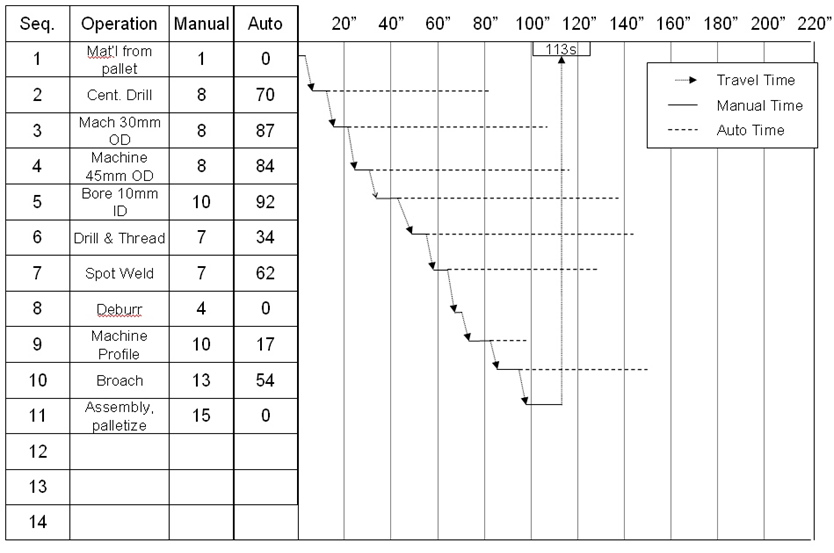
Seq. | Oper | Man | Auto | Cycle |
---|---|---|---|---|
1 | Mat’l from pallet | 1 | 0 | 3 |
2 | Center drill | 8 | 70 | 13 |
3 | Machine 30mm OD | 8 | 87 | 23 |
4 | Machine 45mm OD | 8 | 84 | 33 |
5 | Bore 10mm ID | 10 | 92 | 45 |
6 | Drill & Thread | 7 | 34 | 54 |
7 | Spot Weld | 7 | 62 | 63 |
8 | Deburr | 4 | 0 | 69 |
9 | Machine Profile | 10 | 17 | 81 |
10 | Broach | 13 | 54 | 96 |
11 | Assemble, Palletize | 15 | 0 | 113 |
Leave a Reply