Your cart is currently empty!
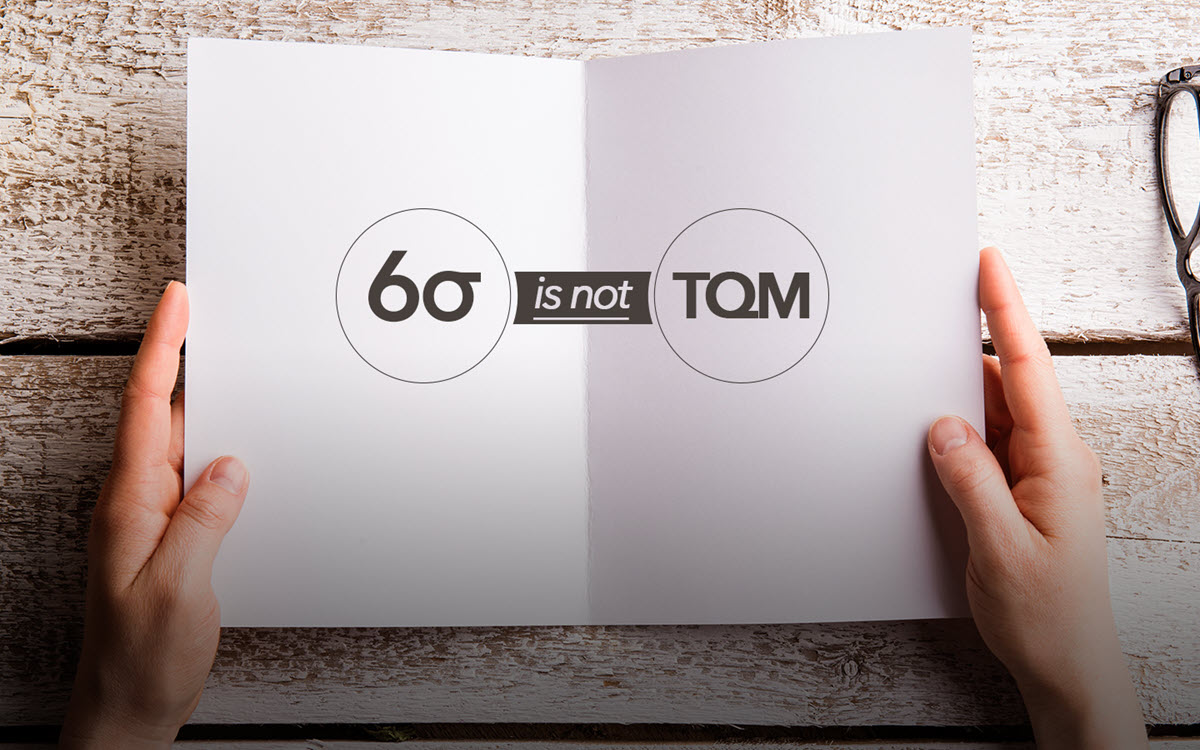
Is Six Sigma the Next Step in Quality Enhancement?
Understanding the distinctions between Six Sigma and Total Quality Management (TQM)
In my previous post, ‘Why Six Sigma Is Not TQM‘, I proposed that Six Sigma is inherently distinct from Total Quality Management (TQM) in numerous ways. This assertion evoked diverse responses from many readers, some disagreeing with certain points I put forth. While I concede that there’s considerable overlap, and a well-executed TQM program can indeed mirror a well-executed Six Sigma initiative, I maintain my stance that Six Sigma is not merely an extension of TQM. It’s noteworthy that Motorola, the pioneer of Six Sigma, also secured the esteemed Malcolm Baldrige National Quality Award, a significant recognition in TQM.
However, Six Sigma is more than a variant of TQM. Its unique internal organizational infrastructure sets it apart. Forget momentarily the charming ‘belt’ terminology associated with Six Sigma and ponder over the groundbreaking roles it has introduced: full-time change agents accounting for roughly 1% of an organization’s workforce, though temporary. This figure is even larger when considering only the professional staff. These individuals signify organizational slack, focused not on routine work output, but on driving change. Their performance evaluation is tied to their innovation, reflecting as tangible improvements benefiting customers, employees, or shareholders.
The negative reactions to these ‘newcomers’ from many quality professionals took me by surprise initially. However, upon reflection, it’s understandable. While these professionals have championed change for years, they’ve traditionally been at the helm of driving it. Six Sigma shifts this dynamic, often putting the quality department at the receiving end of change. Six Sigma initiatives are frequently led by individuals outside the quality department, involving contributors who are not from the ‘quality fraternity’.
Consider this comparison: ASQ Certified Quality Engineers (CQEs) and Six Sigma Black Belts (BBs). The emphasis on measurable, tangible outcomes is a prominent distinction between BBs and CQEs. But what triggers these differences? I propose it lies in the fundamental disparity between Six Sigma and other quality initiatives. Six Sigma is not merely a ‘quality initiative’. Appreciating the contrast between Six Sigma and ‘quality’ is crucial to understanding that Six Sigma symbolizes a paradigm shift in quality as we’ve known it.
Quality | Six Sigma |
---|---|
A functional specialty within the organization | An infrastructure of dedicated change agents. Focuses on cross-functional value delivery streams rather than functional division of labor. |
Focuses on quality | Focuses on strategic goals and applies them to cost, schedule and other key business metrics. |
Is done because โquality is goodโ | Is done because it creates a tangible benefit for a major stakeholder group (customers, shareholders, or employees). |
Loosely monitors progress toward goals | Ensures that the investment produces the expected return. |
People are engaged in routine duties (planning, improvement and control). | โSlackโ resources are created to change key business processes and the organization itself. |
Emphasizes problem solving | Emphasizes breakthrough rates of improvement (e.g., 10X improvement every two years) |
Focuses on standard performance (e.g., meeting requirements, ISO 9000) | Focuses on world-class performance (e.g., 3.4 PPM error rate) |
Quality is a permanent, full-time job. Career path is in the quality profession. | Six Sigma job is temporary. Six Sigma is a stepping-stone; career path leads elsewhere. |
Provides a vast set of tools and techniques with no clear framework for using them effectively. | Provides a selected subset of tools and techniques and a clearly defined framework for using them to achieve results (DMAIC) |
Goals are developed by the quality department based on quality criteria and the assumption that whatโs good for quality is good for the organization. | Goals flow down from customers and senior leadershipโs strategic objectives. Goals and metrics are reviewed at the enterprise level to assure that local suboptimization does not occur. |
Developed by technical personnel | Developed by CEOs |
Focuses on long-term results. Expected payoff is not well-defined. | Six Sigma looks for a mix of short-term and longterm results, as dictated by business demands. |
If Six Sigma represents the future of quality enhancement, those in the quality profession may need to refrain from criticizing it and adopt a more long-term perspective. CQEs who face rejection as BB candidates should introspect on the additional knowledge, skills, abilities, and personal traits required to be successful BBs. Some CQEs tend to behave as though barriers still exist long after they’ve been removed. There’s a lack of realization about the need to express their results in terms of the bottom line. They need to understand that improving quality is not an objective in itself; it’s a tool to achieve broader goals.
Leave a Reply