Your cart is currently empty!
Six Sigma: Love It or Hate It?
For a technical topic, Six Sigma tends to generate a lot of strong feelings. As the author of The Six Sigma Handbook I obviously have a few of these feelings myself. Still, on balance, I’m a Six Sigma “lover.” I think that the approach is an excellent way to help organizations achieve their goals by improving their core processes. However, I am not blind to the fact that Six Sigma also has its dark side. Here are a few examples that leap readily to mind.
Six Sigma Everywhere
Some organizations apply Six Sigma where it really shouldn’t be applied. For example, one of my clients tried to apply it to an R&D operation. The poor folks trying to create something brand new from scratch were forced to try and figure out how to measure their progress, submit regular reports, track metrics on control charts, show process improvements, etc. It was a disaster.
Six Sigma is a process improvement methodology, and it generally does this by reducing variation and eliminating errors and waste. Creativity involves innovation and risk taking. It deliberately introduces variability by changing things to try and discover something new. It is inherently and unavoidably wasteful. There is no process for understanding inspired creativity and it can’t be quantified until after it has generated failures and successes. The value of innovation can’t be measured until after something great has been achieved, and it’s not possible to tell if you’re 1% of the way to the achievement, or 99%. You won’t know until you get there.
The Six Sigma Elites
Six Sigma has an infrastructure of “Belts” that can have an air of elitism about them. Of course, there is also an air of elitism around other groups within an organization. In manufacturing it is the engineers, in healthcare the physicians, in insurance the actuaries. Why all of the animosity towards the Belts? My theory is that it happens so fast, and it happens to people who already have a defined status in the organization. One minute John or Jane are ordinary blokes, the next they are exalted Black Belts. What’s up with that? To help promote Six Sigma in organizations just starting the initiative, the newly minted Belts are announced on the company web site and written about in the company newspaper.
To make matters worse, the group of Belts use jargon that others can’t understand and, frankly, some of them lord their new status over others. For some practical advice on this subject, see the excellent technical paper titled At the Corner of Lean Street and Statistics Road, available in the archives of the 2020 JMP Discovery Americas Summit. Here’s a snippet, used with permission.
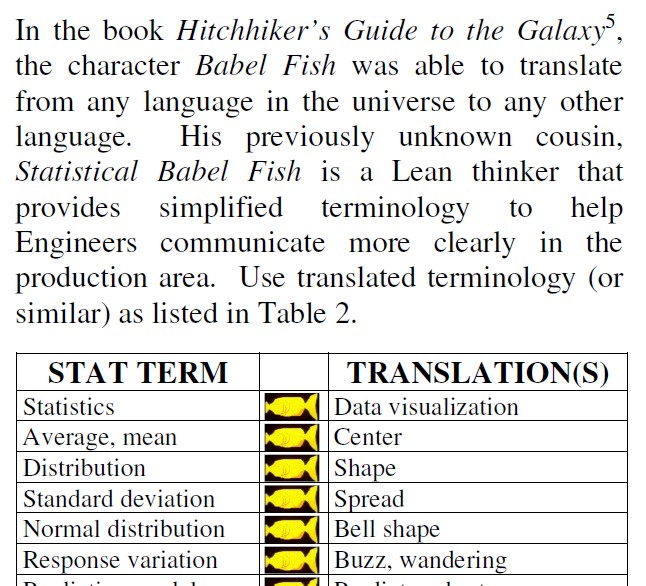
Still, having this cadre of people whose job it is to pursue change project is perhaps the single most important thing that made Six Sigma work where TQM and other change initiatives failed. Organizations didn’t just mouth nice sounding words about the importance of change, they put their resources where their mouths were. They rolled up their sleeves and they got to work.
Most People Donโt Like Change
In my boyhood home of Nebraska there was a common saying, “If it ain’t broke, don’t fix it.” The message was clear: don’t change anything unless it is absolutely necessary. The problem with this approach is that, in a world where your competitors are changing things at a rapid rate, if you wait until the need for change is painfully obvious, you may be too late.
Nobody Wants Someone Telling Them How to Do Their Work
If you’ve been doing a job for a while, chances are you’ve become pretty good at it. No matter how much training you received, you learned a lot from the school of hard knocks. Now along comes this bunch of outsiders telling you that they have a better way of doing things. The reaction? Yeah, Right! If the team knows what they’re doing they will ask you for your input and they will use it to make your job easier or better. But if they don’t, they’ll make it harder and less pleasant. A great way to look at the role of the Six Sigma Belt is shown in Figure 2
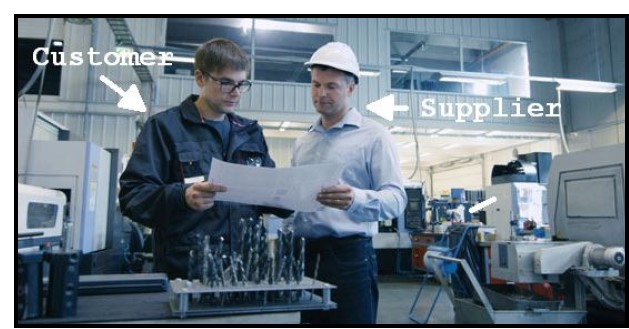
Fear of Job Loss
It can be frightening to see how much waste there actually is in some systems. I’ve seen departments with 25 people before a Six Sigma project and 5 afterwards. The smart company will plan for this kind of impact and have new jobs for those no longer needed. But many companies simply let the displaced people go. It’s no wonder that the result is fear of Six Sigma shining a light into your work area.
Unintended Consequences
Sounds like a great idea, with the best of intentions, what could possibly go wrong? In reality, if the Six Sigma team isn’t extremely careful, Six Sigma projects can break one thing as they improve another. The control phase of the project is supposed to prevent this from occurring, but sometimes it happens anyway. Despite all efforts there will be times when changing something results in unforeseen problems, it is the nature of change. When it happens, it will produce resentment.
In many cases, Belts can avoid unintended consequences by including everyone they can think of in their stakeholder communication plan and listen carefully to all concerns.
Six Sigma Is Used When a Simpler Approach Wouldโve Worked Just As Well
Six Sigma DMAIC or DFSS projects have their rightful place. But let’s face it, the Six Sigma approach is a problem-solving sledge hammer. Sometimes a fly swatter is more appropriate.
Six Sigma People Get Credit for Ideas Originally Conceived by Others
One of the main bailiwicks of Six Sigma is the problem that has been “solved” over and over again. When chronic problems are attacked by Six Sigma teams it is almost certain that the final solution will incorporate elements of things that were proposed, and maybe even tried, in the past. The people who had thought of the the fix before the Six Sigma team probably tried and failed to get their solutions implemented. Six Sigma tends to receive more resources and management support than lone problem solvers. The resulting hurt feelings can be ameliorated-but not eliminated-by recognizing those who tried to raise the flag in the past. Better yet, when it’s time for the inevitable project pizza party, Belts can state clearly that the front line operators and maintenance people were the ones that got it done and that we (Belts) served only in a support role.
Summary
While some of these things can be avoided, Six Sigma will always have its dark side. Six Sigma is all about change and change is inherently risky. However, change is also vital to survival. The battle between stagnation and chaos is never ending.
Leave a Reply