Your cart is currently empty!
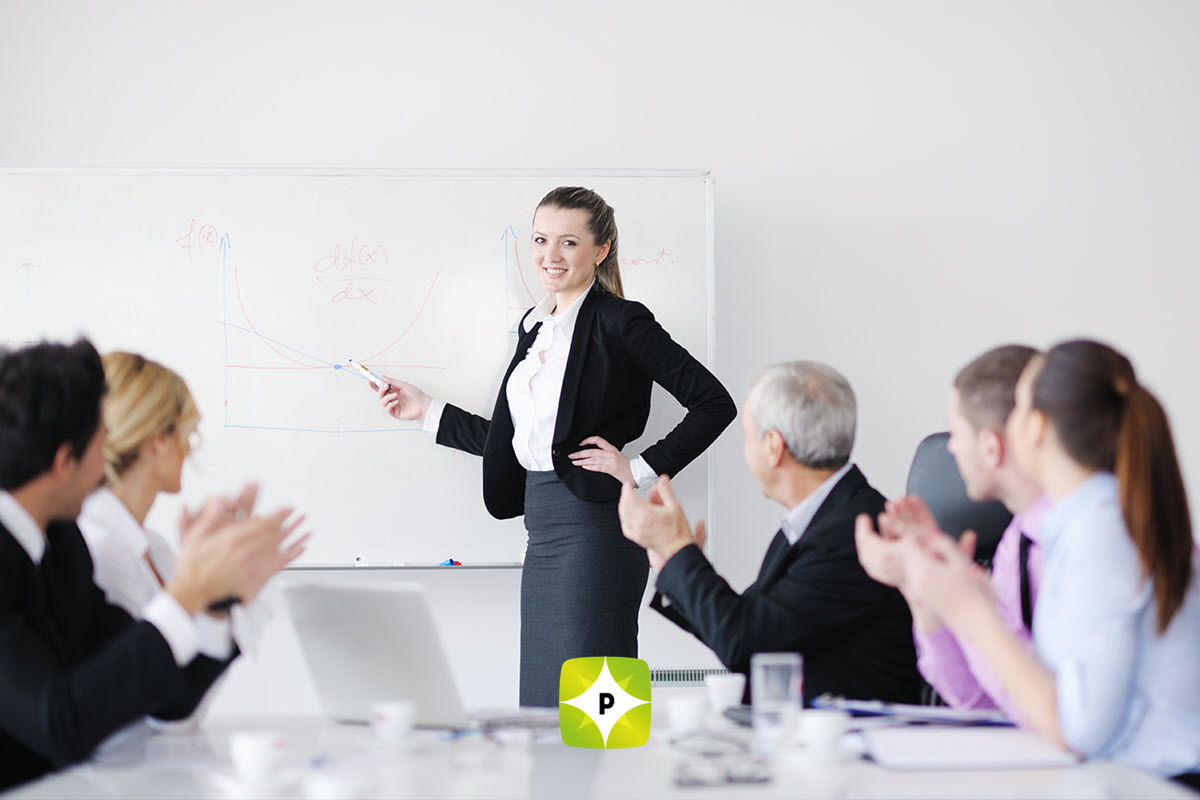
Cargo Cult Six Sigma
In the South Seas there is a cargo cult of people. During the war they saw airplanes with lots of good materials, and they want the same thing to happen now. So theyโve arranged to make things like runways, to put fires along the sides of the runways, to make a wooden hut for a man to sit in, with two wooden pieces on his head to headphones and bars of bamboo sticking out like antennas heโs the controller and they wait for the airplanes to land. Theyโre doing everything right. The form is perfect. It looks exactly the way it looked before. But it doesnโt work. No airplanes land. So I call these things cargo cult science, because they follow all the apparent precepts and forms of scientific investigation, but theyโre missing something essential, because the planes donโt land.
Richard Feynman, Cargo Cult Science, 1974
When, therefore, a man absorbed in the effect which is seen has not yet learned to discern those which are not seen, he gives way to fatal habits, not only by inclination, but by calculation.
Frederic Bastiat, That Which is Seen, and That Which is Not Seen, 1850
It seems as if the business improvement world has more than its share of fads. Over my career, Iโve encountered statistical quality control, zero defects, quality circles, Deming/SPC, Motorola Six Sigma, TQM, business process re-engineering, Lean, GE Six Sigma (with Belts and other infrastructure), and various combinations and permutations of these. In our field, the MTBF (mean time between fads) is roughly four years, nearly half the seven-year MTBF for the business community as a whole. With this large sample size (n = 9 isnโt that bad), Iโve been able to discern a pattern in the life-cycle of a fad:
- An isolated group off somewhere in the organization is doing something thatโs producing excellent local results. They are discovered by others.
- A champion helps to spread the groupโs message to the larger organization, and results appear there too.
- Outside organizations discover the secret and are able to replicate the results. A really big company or other prestigious source begins to tout the approach.
- The bandwagon starts to roll. Others get on board and shout their success stories to the business media.
- As demand for information on the new approach builds, the supply of talented people who understand the details is exceeded. Suddenly, people who hadnโt heard of the new approach a year ago, or who are familiar with only some of the details, are supposed experts.
- Everyone is doing it. The new approach is widely discussed in the non-business media.
- Stories begin to appear about how โExecutives report that 80 percent of the attempts to do X result in failure.โ First just a trickle of stories, then a flood.
- Mainstream academic institutions begin to teach the approach.
- It becomes accepted dogma that โX doesnโt work.โ
- On to the next fad.
As someone who follows Six Sigma news closely, it appears to me that the approach is nearing the end of its life-cycle. As an advocate of Six Sigma for traditionally managed companies, I find this somewhat distressing. After all, there are certainly thousands of firms that could benefit from the additional rigor Six Sigma brings into the business. This is especially true of non-manufacturing firms in general, and those health care in particular. As I get older I grow increasingly concerned that someday Iโll need to go to a hospital with a minor problem, only to be killed by a medical error. So, in my own self-interest, Iโve decided to see if I can offer some suggestions to arrest the decline and fall of Six Sigma by identifying its root cause.
Six Sigma: form vs. substance
The problem begins at step 5. The pseudo-experts look at Six Sigma and they see Champions, Master Black Belts, Black Belts, Green Belts, DPMOs and a plethora of statistical tools. They see projects and all of the affiliated trappings: sponsors, teams, Gantt charts, milestones, financial validation, and software to track the project portfolio and summarize results. They see lots and lots of Six Sigma training and software and meetings. They see โsupportโ from top leaders.
These are the visible forms of Six Sigma. They can be easily copied, but they wonโt bring the planes in. They are not the Six Sigma that returned Motorola to competitiveness for a decade and extended the GE miracle. This is Cargo Cult Six Sigma.
What is Six Sigma, really?
Six Sigma is clarifying the desired outcomes for all stakeholders, identifying the drivers and root causes necessary to achieve them, using data wisely to help guide companies as they try to address root causes, and using a systematic approach to continuously improve.
Six Sigma uses a rigorous, focused and highly effective implementation of proven quality principles and techniques. Today, this means that Six Sigma is deployed by training a small cadre of in-house technical leaders, known as Six Sigma Black Belts, to a high level of proficiency in the application of a selected subset of project management and statistical tools. These change agents are supported by an infrastructure of leaders known as Champions and technical specialists known as Master Black Belts. The tools are applied within a simple performance improvement framework known as Define, Measure, Analyze, Improve, Control, or DMAIC (a related approach, Design for Six Sigma, or DFSS, is also gaining favor). Six Sigma operates in a culture of willingness to change and tolerance for mistakes, which are inevitable when change occurs. The leaders of Six Sigma organizations build and maintain this culture.
Note that what Six Sigma is and how Six Sigma is deployed are two entirely different things. Cargo Cult Six Sigma misses what Six Sigma is and completely focuses on the visible aspects of Six Sigma. The short-term results are abysmal. The long-term result is to find yet another fad and start the whole process over again.
Epilog
This isnโt the first time: Before Cargo Cult Six Sigma, we had Cargo Cult SQC, zero defects (which was almost itself Cargo Cult management,) quality circles, and so on. The problem appears to be inherent in business management culture. I discuss the solution (i.e., getting rid of management) in my book The End of Management (Atlantis Pub, 1999). However, until this can be done, organizations need to operate using the best known management approach. At the moment, thatโs still Six Sigma.
Leave a Reply